Field Data Collection
Uninterrupted Tracking and Efficiency Management in Production
Reducing Losses in Production and Increasing Efficiency
Businesses encounter various losses during their production. Production lines established due to poor quality, failures, rework, scrap, speed losses are the realities of daily life.
In today’s competitive world, the most important goal of businesses is to increase productivity and gain an advantage over their competitors. What is important is not how much you produce and/or how fast you produce, but rather how much loss you produce. Reducing losses is the main problem that businesses struggle with.
The first goal is to create an efficient and low-loss production infrastructure. The first step to achieve this is to collect and process the information on the production line in a healthy way and to reach the results that will guide the business. In other words, it is necessary to act with the fact that what cannot be measured cannot be improved .
From this collected data, it is necessary to understand the factors and situations that cause the loss of machinery and equipment, employees’ time, what are the factors affecting OEE and how they should be monitored.
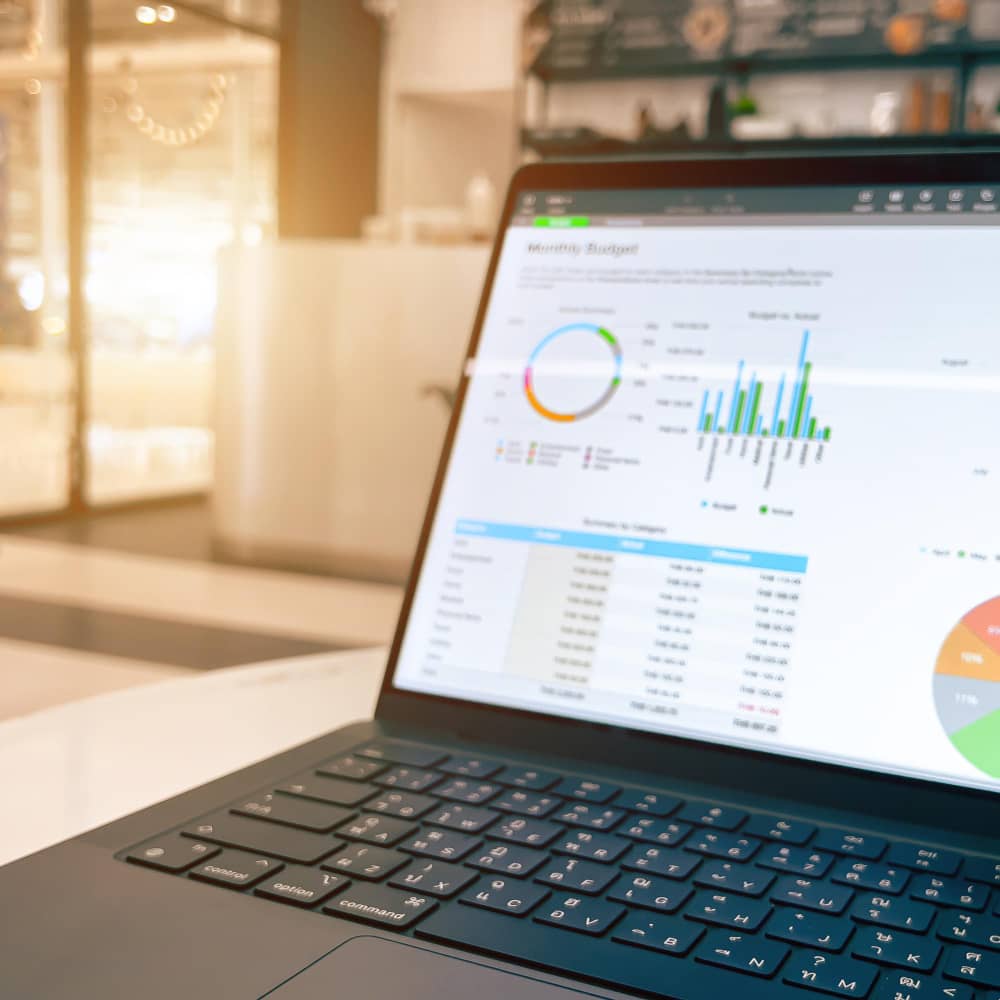
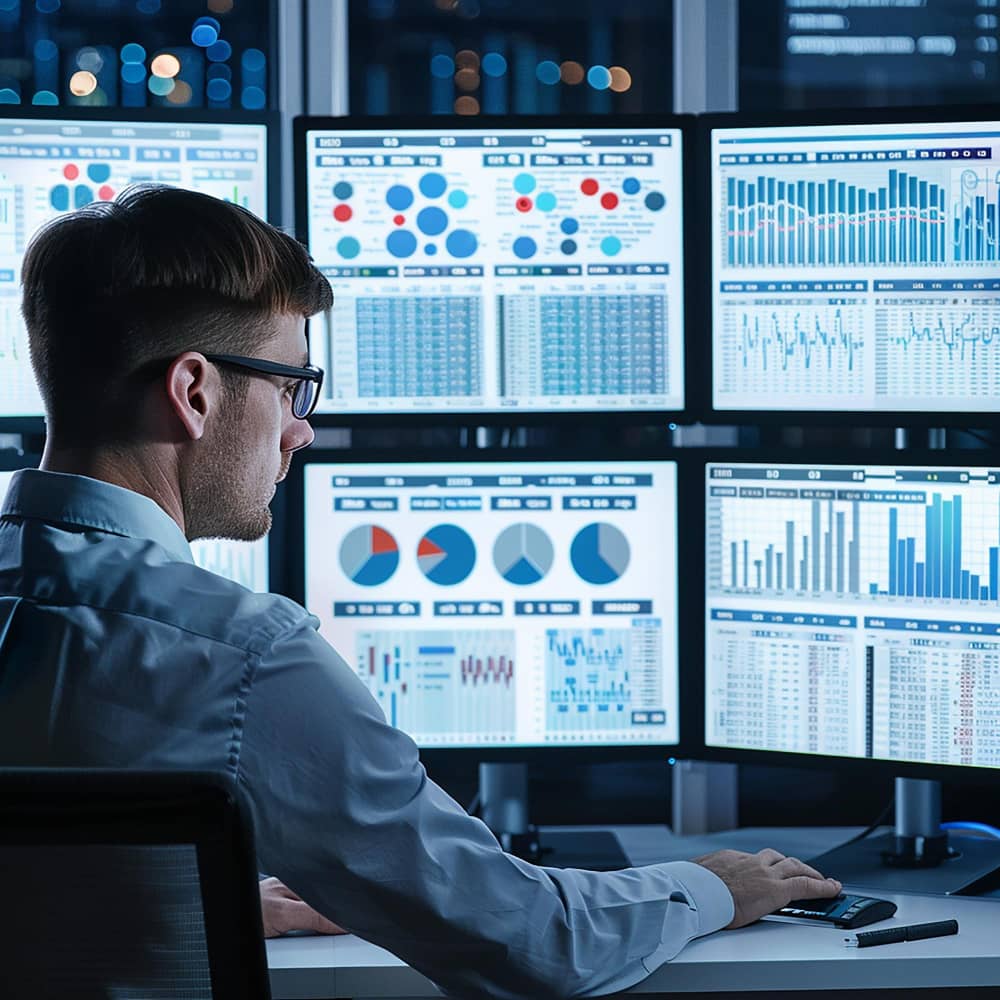
Accurate and Timely Collection of Production Data
In addition to the collection of scalable production data, the basic rule for the correct functioning of any production management system and the associated production planning subsystem or quality management system is the timely closure of opened work orders as the relevant operations are completed. In other words, production confirmations from the production site must be received on time and accurately.
According to the characteristics of the operations performed in the production processes (manual, semi-manual, fully automatic machine or bench use), it should be determined how to receive production confirmations of work orders.
Production confirmations can be obtained using mobile devices, touch screens or a computer. Which of these methods will be used should be decided in the relevant project.
With BSOFTvt Production Data Collection System software, you can track the downtime reasons, failure causes and durations, productivity of a work machine, operator, material, production line. And you can access this information instantly with dozens of ready-made reports. And BSOFTvt Field Data Collection Software provides an interface that integrates the work machine, operator and ERP system.
Electronic Monitoring of Production Activities and Increased Efficiency
The aim is to electronically record the production activities of the lines and/or independent machines formed by machines integrated with each other in production facilities during the day, to reveal the reasons why they stop and how the lost time caused by these stops affects the “efficiency” and thus to contribute to the profitability of your business by providing a rapidly increasing efficiency in production.
It is a 100% web-based software with a flexible, parametric and modular structure, consisting of application modules that work integrated with each other and developed using microsoft ASP/ASP.NET technology. Its main functions are data collection, data analysis, reporting and decision support systems.
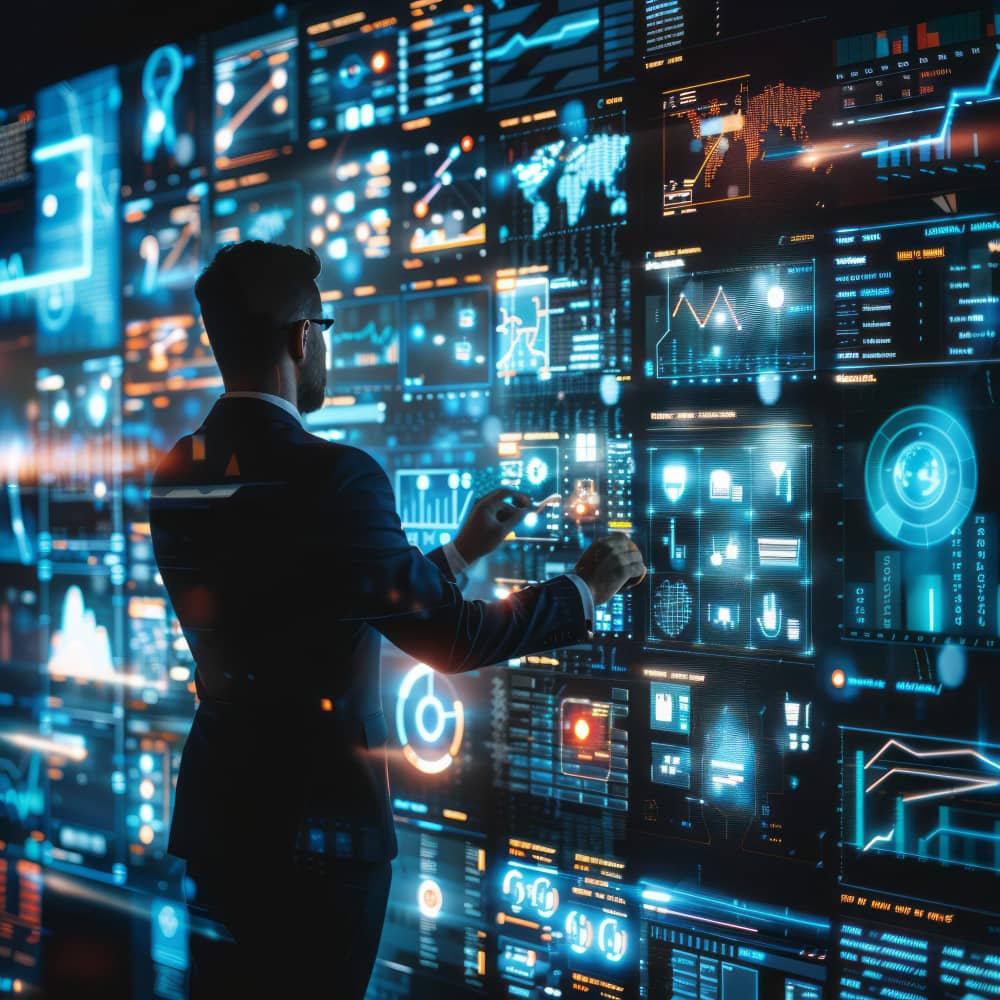
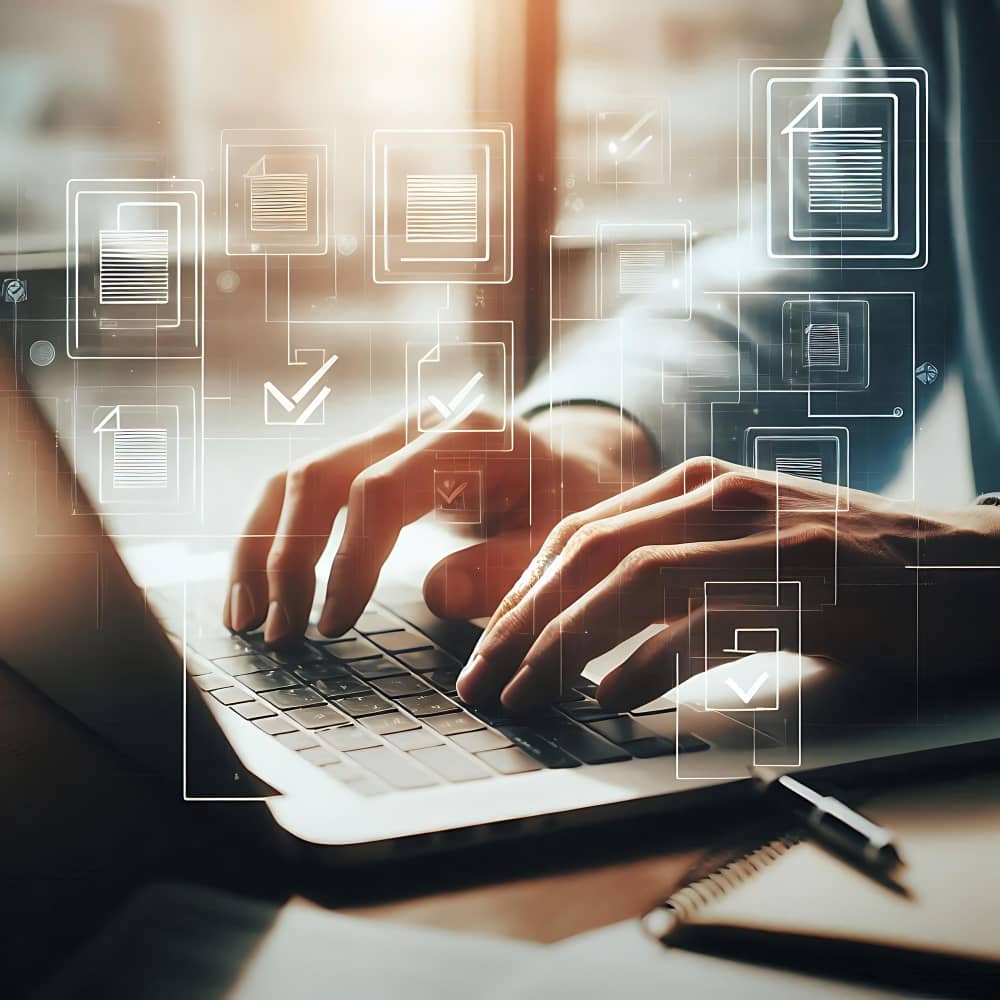
Benefits of BSOFTvt Production Data Collection System
It is possible to summarize the benefits of BSOFTvt Production Data Collection System as follows;
- You can track production status, quantity and duration in real time.
- You can instantly monitor the material flow in your production processes.
- You can see stop times, stop types, stop distributions in detail.
- You can track raw materials and intermediate products used in your production process.
- You can report OEE, performance, capacity utilization tracking.
- You can track staff working time and efficiency.
- You can monitor instant production performance tracking via Dashboard.
- You can track production, maintenance and quality processes.
- You can enter production operation processes in detail.
- You can automatically collect data from PLC devices, sensors and RFID devices.
- You can collect data with handheld terminals and mobile devices with the help of an operator.
- You can integrate with different ERP packages.
OEE: A Method for Measuring
and Improving Equipment Effectiveness
It is the best measurement method to observe and improve the efficiency of production processes (machines, production centers, assembly lines, etc.). It is one of the most frequently used maintenance indicators in the industry and one of the tools used in lean production practices.
OEE is often used as key data for TPM (total productive maintenance) and Lean Manufacturing. It is of great help in measuring the effectiveness of TPM. It was developed as part of the TPM process and is the primary performance measurement method.
The aim is to focus on improving the performance of existing machinery and equipment instead of making unnecessary purchases. The data required for OEE calculation is already kept by many businesses. With OEE, it is possible to turn this data into a KPI that tracks the overall performance of the business. OEE is a tool that can be used in areas other than manufacturing.
In short, OEE is the measurement of how effectively time is used to produce a quality product. The higher the OEE value, the more effectively the equipment is used. Equipment efficiency means that the equipment produces the desired quality product at the planned speed within the planned production time without any unplanned downtime. Therefore, increasing equipment efficiency is only possible by reducing losses.
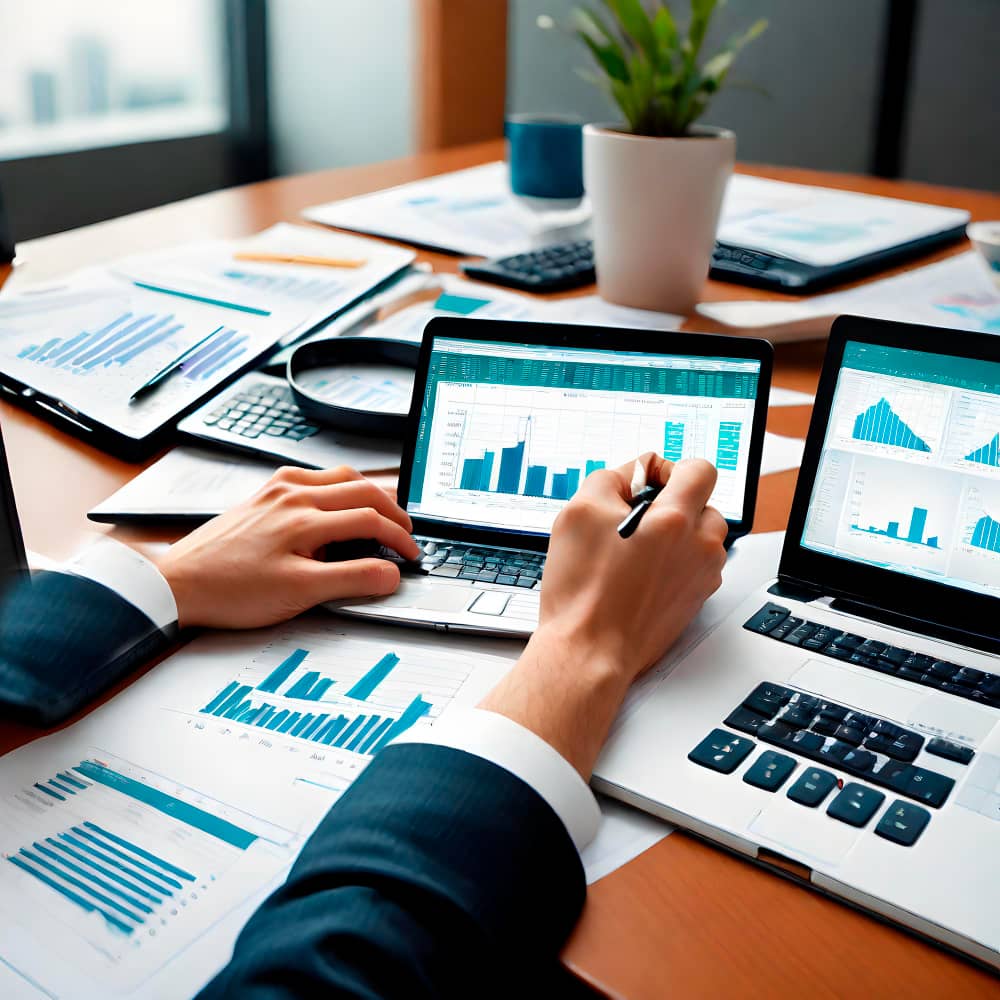
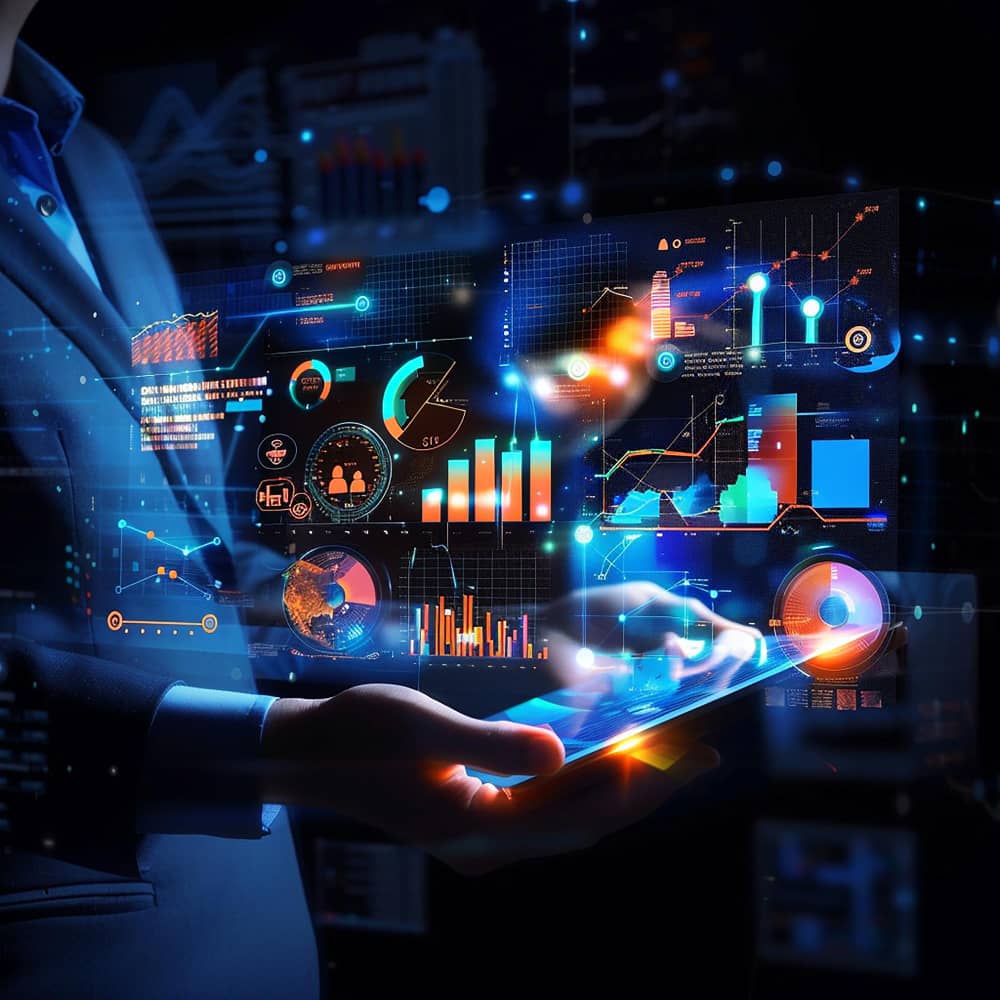
Improving Equipment Performance with OEE
and Productivity Tracking
The International Optimum Oee value is considered to be 85% and above.
OEE is very important in terms of revealing equipment conditions. Furthermore, OEE clarifies the identification of weak points in order to reach optimum equipment conditions. In doing so, it focuses on eliminating factors such as unexpected breakdowns, speed losses and quality losses in the process. Maximizing equipment effectiveness depends on eliminating the 6 major losses that affect equipment performance throughout the company.
The OEE indicator is one of the most prioritized indicators in all advanced manufacturing companies today. OEE gives very clear information about the overall performance of the factory and equipment efficiency.
The machinery and equipment used in today’s industry have high speeds and cause large changes in production values in small time periods. Therefore, machinery and equipment are of great importance in product increase. In today’s market where competition is getting tougher every day, the effective use of machinery and equipment is vital for businesses to reduce their costs. This can be realized with OEE. It is a measurement technique that shows how much the business can utilize the equipment and can be the basis for improvement efforts.
OEE and Total Efficient Maintenance: A Strategy to Improve Equipment Effectiveness
One of the main objectives of Total Efficient Maintenance is to maximize the value of equipment effectiveness for business assets. OEE is expressed as a measure used to determine the efficiency of the equipment used in the enterprise. In particular, companies in the manufacturing sector state that the analysis conducted within the framework of OEE improves the useful utilization rate of their assets. Total equipment effectiveness is an important parameter that measures the efficiency with which machines and facilities are used and plays a key role in the success of lean production and total efficient maintenance practices.
OEE is an industrially recognized, valid measure of performance.
We can show the general formula for OEE as follows:
OEE= Availability x Productivity x Quality
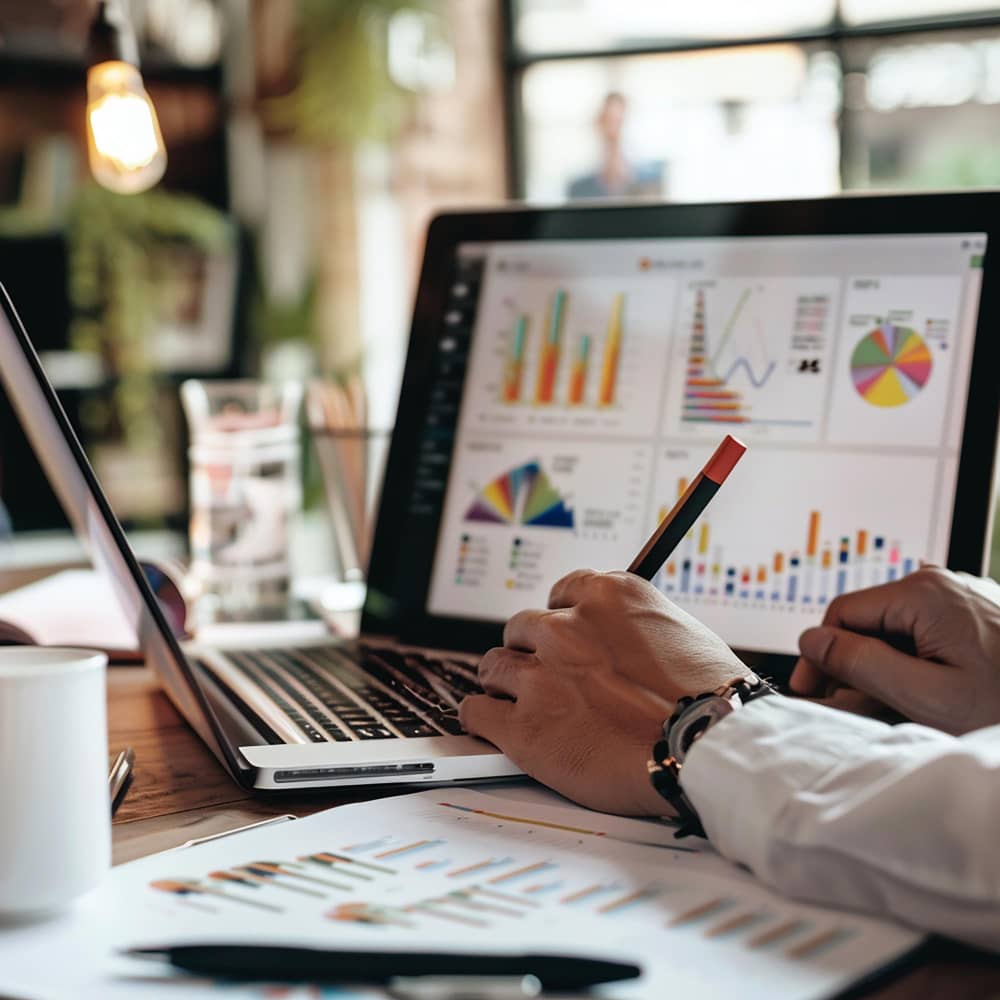
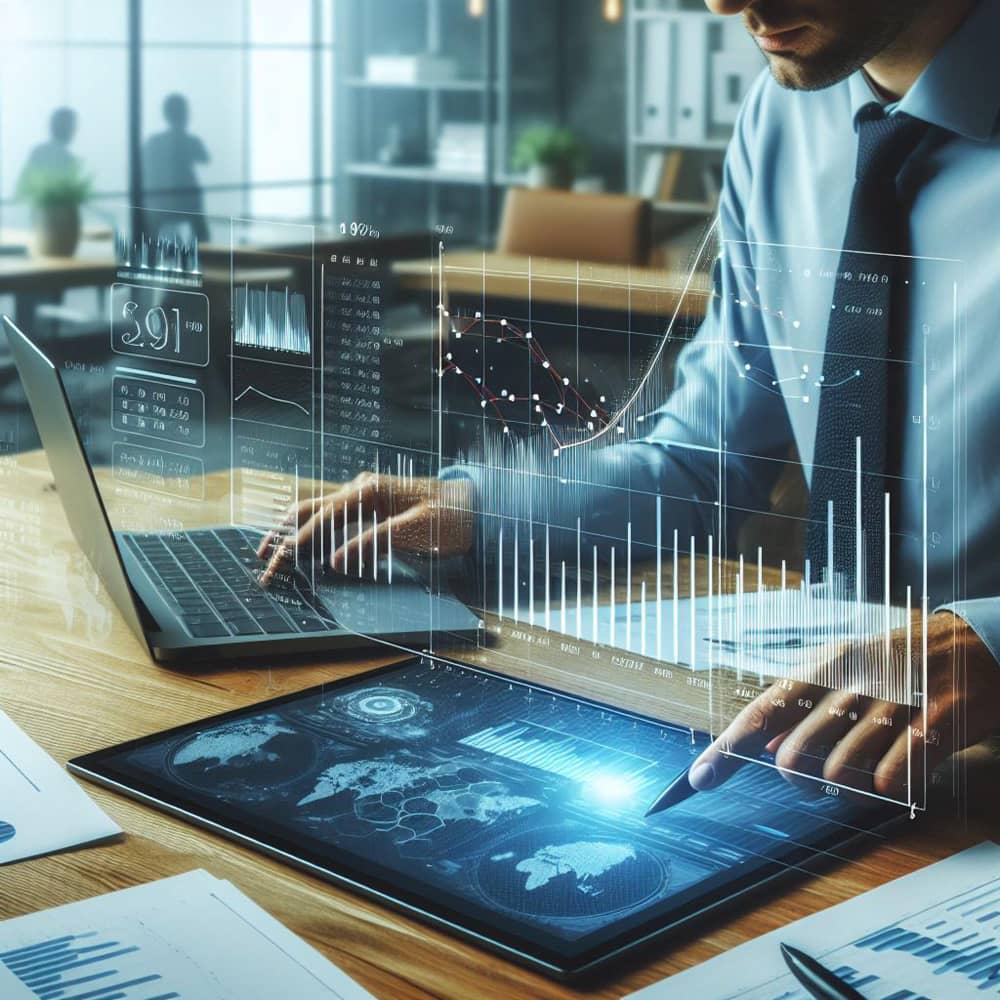
Available Time (Availibility)
This term is used to calculate how long the production machine runs during production (availability). The purpose of this calculation is to calculate the actual usable time of the machine during that day. For example, in one day, our machine is ready to work for 24 hours (1440 minutes). However, during this time, we only used this machine for production for 18 hours. This means that the available time is 75% (18/24). These 6 hours of lost time could be due to machine maintenance, lunch break, machine breakdown. Or the factory may have decided not to run the machine for 6 hours. But this is usually not used in the calculation.
The pause times we should consider when calculating availability can be
- Food break
- Cleaning
- Planned maintenance
- Machine failure
- Type change (Change over)
- Pauses
- Quality problems
As can be seen, these downtimes can be classified as planned or unplanned, or forced or avoidable.
Productivity
Productivity, also defined as performance, is calculated by calculating the ratio of the production amount of our machine within the given time period to the maximum production capacity amount.
Let’s assume that our machine produces 60 parts per hour, but the full capacity of our machine is 80 per hour. This means that (60/80) our machine works with 75% performance.
The biggest performance degraders are reworked parts (remakes) and faulty parts.
Quality
In OEE, quality is calculated as the ratio of defect-free parts to defective parts produced within a given time period. Suppose we produce 100 parts and 90 of them are usable, which means that our quality is 90%.
If we combine the above examples in the formula, we get the following result:
OEE= 75% x 75% x 75% x 90% = 51
As you can see, our OEE percentage is quite low, according to international production standards, 85% – 90% OEE is in the best in class category, in order to achieve this, our machine has to produce quality material every minute within the given time.
We can also calculate OEE in a different way by simply dividing the time required to produce quality parts by the net available time. In this case the result will be the same.
Let’s try to clarify the issue with one more example:
In a factory with an 8-hour shift, 2 10-minute breaks and a 5-minute cleaning period, the production plan is as follows:
Cycle time : 10 seconds
Realized Production: 2240 units
Number of Scrap 50 pieces
Unplanned Pause Time: 32 minutes
Let’s make our calculations accordingly:
Planned Time (All Available Time) = 8 hours = 8 x 60 = 480 minutes
Planned Stops 2 breaks x 10 minutes + cleaning time 5 minutes = 25 minutes
Net Available Time = 480 – 25 = 455 minutes
Unplanned Stops = 32 minutes
Net Operational Time = Net Available Time – Unplanned Stoppages = 455 – 32 = 423 minutes
Time Spent for Whole Production: 2240 total parts x 10 seconds = 22400 / 60 = 373.33 minutes
Lost Time due to Scrap: 50 scrap pieces x 10 seconds = 500 / 60 = 8.33 minutes
Now we can calculate OEE:
Availability = (423 / 455) x 100 = 92.97
Efficiency = (373.33 / 423 ) x 100 = 88.26
Quality = (373.33 – 8.33) / 373.33 * 100 = 97.77%
OEE = 92.97% x 88.26% x 97.77% = 80.22
Let’s check our calculation using the second way mentioned above:
Only the time needed to produce quality parts / net available time
OEE = [ (373.33 – 8.33) / 455 ] x 100 = 80.22
If used correctly OEE is really a very efficient concept for lean production, one of the reasons is that a well analyzed OEE report shows us why we are not achieving the desired quantity in production time, why there are too many machine breakdowns and other reasons. This information gives us an excellent communication opportunity for machine operators, sales people, maintenance and repair people to make the necessary improvement plans.
Documents
There are no recorded documents.
Modules
Data Collection Processes
It is very important that the data to be collected from the workbenches (work machines) in the production areas with DATA COLLECTION DEVICES are taken online or online according to the need and transferred to the computer environment, monitoring the work machines, personnel and producing reports on productivity. Because, in today’s world, many businesses are in an effort to improve their productivity and are naturally faced with the need to collect data from production and analyze this data.
With the Data Collection Operations software, which is the main module of BSOFTvt Production Data Collection System, you can instantly collect data from the field, production lines and machines, process and transform this collected data into meaningful data and process it into the database. BSOFTvt Data Collection Operations module is a 100% web-based software where you can monitor production parameters in real time.
With BSOFTvt Data Collection Operations module , all kinds of information such as production type, production quantity, type, frequency, unit time, reasons for stoppage, stoppage times, intervention waits, intervention times, job changes, job change times, worker, technician, master identities, interventions, etc. of production lines are collected automatically in a detailed, lean and ergonomic manner.
Raw data collected from production is transformed into meaningful data using different algorithms. When unexpected values are encountered during the data collection phase, the information engine within the system is activated and necessary warnings are made. Thus, it is ensured that unexpected results are instantly informed and prevented.
The structure of the hardware/devices to be used for data collection is decided after the production site inspection in the enterprises. BSOFTvt supports the following methods in data collection processes.
- Data collection from sensors, encoders and PLC devices
- Automatically collect data from RFID devices
- Data collection with handheld terminals and mobile devices with operator assistance
- Data collection with operator assistance through operator panels (kiosk)
- Support for up to 32 devices on one line
- Substructure with 0.25 nyaf cable
System Structure:
- Parameters such as shift, department, fixed values within the workplace are defined.
- Score definitions corresponding to the work done are made here.
- Questions for step skipping are defined.
- Define parameters for OEE generate reports.
- Location mappings are made with personnel, thus limiting the locations where each personnel can enter records.
- Data terminals connected to production machines automatically monitor production and data can be entered with a barcode reader or keypad.
- Operators start work at the beginning of the shift by entering their registration numbers into the system. Other operators who take their places during breaks are monitored, working time, break time, etc. are monitored.
- When the production of the work order produced in the planning unit is started in the enterprise, the work order number is entered in the terminal on the relevant machine. The ongoing production movement is automatically counted to this work order.
- When there is no production signal from the workbench, it can be automatically detected that a stop has occurred and an alarm is generated.
- The technician who comes to intervene in the fault enters his/her own registration number and error code from the terminal, the intervention time is thus tracked. Intervention (arrival at the workbench) and processing times can be monitored.
- Depending on the circumstances, work orders can be partially or fully completed. And, completed work orders are recorded in ERP.
- Productivity information from BSOSTvt-enabledwork centers is instantly transmitted online via monitors to operators and managers.
- Events such as malfunctions, downtimes and inefficient operation can be immediately sent as a warning to the desired persons via the notification engine (sms, e-mail, etc.).
- Thanks to online monitoring, disruptions in production can be intervened immediately and problems can be eliminated.
Some of the gains you will get when you track production performance through BSOFTvt Data Collection Operations module;
- Production time, quantity and instant tracking
- Instant tracking of stops and wastage
- Capacity and performance monitoring
- OEE Tracking
- Monitoring staff working time and productivity
- Instant production performance monitoring via Dashboard
- Ensuring the integration of production operation and product tree operations with the commercial package used.
Online Monitoring Operations
The instant status of production machines, work centers, production lines, etc. in the enterprise included in the BSOFTvt structure is broadcast online from large monitors or users’ screens. Information that can be monitored online;
- Information on Production (location, type, quantity, work order, unit time, etc.)
- Faults, (Causes, Duration, etc.),
- Stoppages (Reasons, Duration, etc.),
- Job Changes and Job Change Periods,
- Inefficient Studies,
- Operators
- Shift Information,
- Production quantities (planned, produced, remaining, defective production quantities),
- Productivity parameters (OEE, Availability, Performance, Quality),
- Machine production speed, etc.
With the Online Monitoring Module, it is possible to monitor the real-time status of all machines in the factory. By hovering and clicking on the relevant work centers, all information about the relevant work order can be viewed.
It is possible to monitor the status of the machines included in the BSOFTvt structure online in different colors (green, yellow and red).
Data Analysis (OEE+Production) Operations
BSOFTvt Data Analysis Module presents meaningful data collected from the production site in easy, understandable, detailable, user-friendly reports and visual graphics. All reports are created according to the user role, within the authorizations and only visible to the relevant people.
In addition to many ready-made reports in its structure, reports such as OEE (Overall Equipment Effectiveness) and TEEP (Total Effective Equipment Productivity) reports can be easily produced by evaluating different and optional production quantities, downtime, faulty production quantities. With the Report Wizard, reports that can be designed according to the needs can be produced.
OEEs can be reported in detail on machine, operator, production line, shift basis. In detailed and different formatted reports that can be obtained on machine basis, work order, shift, worker basis, etc. Different content can be accessed with many different filters, including OEE calculations.
Comparative productivity reports and change graphs can be prepared for the past. Efficiency reports can be integrated with already used systems, sensors, PLCs, and the outputs can be organized to work in harmony with integrated systems according to the needs.
Using the Report Wizard, different reports can be prepared by shaping the information collected about the production, downtime, scrap production, quality of the enterprise by the user.
The following report types are available in the BSOFTvt Data Analysis Module.
- Efficiency (OEE-EE) reports,
- Fire reports,
- Posture reports,
- Maintenance reports,
- Machine, Production Line based reports,
- Shift, Operator based comparative reports.
ERP Integration Processes
BSOFTvt Production Data Collection System works in an integrated and integrated structure with the ERP systems used by the enterprises.
With web services prepared for different modules (finance, inventory, current etc.), BSOFTvt can exchange 2-way data with ERPs of enterprises according to need. Again, data exchanges between these systems can be online or offline according to the need.
Thanks to this integration, the data in the ERP system (production work orders, etc.) are transmitted to the production site, and the data collected from the production site by automatic or manual methods (production, scrap quantities, operation times, quality values, etc.) are transferred to the ERP system in real time. Depending on the requirements of the enterprises and the ERP setup, the communication structure and the content of the transferred information may change.
Start Your Digital Transformation Journey with Biltaş
Meet smart software solutions that will optimize your business processes and increase your productivity.