TPM Total Productivity Management
Increase Productivity by Implementing Total Productivity Management with BSOFTtpm
Total Productivity Management (TPM) and BSOFTtpm Solutions
In order for our industrial organizations to be successful in both national and international markets by increasing their competitiveness, they need to develop completely and rapidly. This development starts from the factory floor and requires the use of an effective methodology for rapid development.
In addition to management style, the use of methods such as Total Productive Management (TPM) and the encouragement of creativity and participation of all employees in the development of products, production processes, quality, and therefore competitiveness and profitability of the company.
TPM is a maintenance approach that requires the participation of all employees in daily production activities, foresees autonomous maintenance, prevents failures, and maximizes equipment efficiency. In other words, TPM is a methodology used to have strong production capability, reduce losses and increase productivity.
BSOFTtpm is a 100% web-based software developed using microsoft ASP/ASP.NET technology, consisting of many application modules that have a flexible, parametric and modular structure, integrated with each other to ensure the automation of Total Productivity Management (TPM) methods of the industry and production sector.
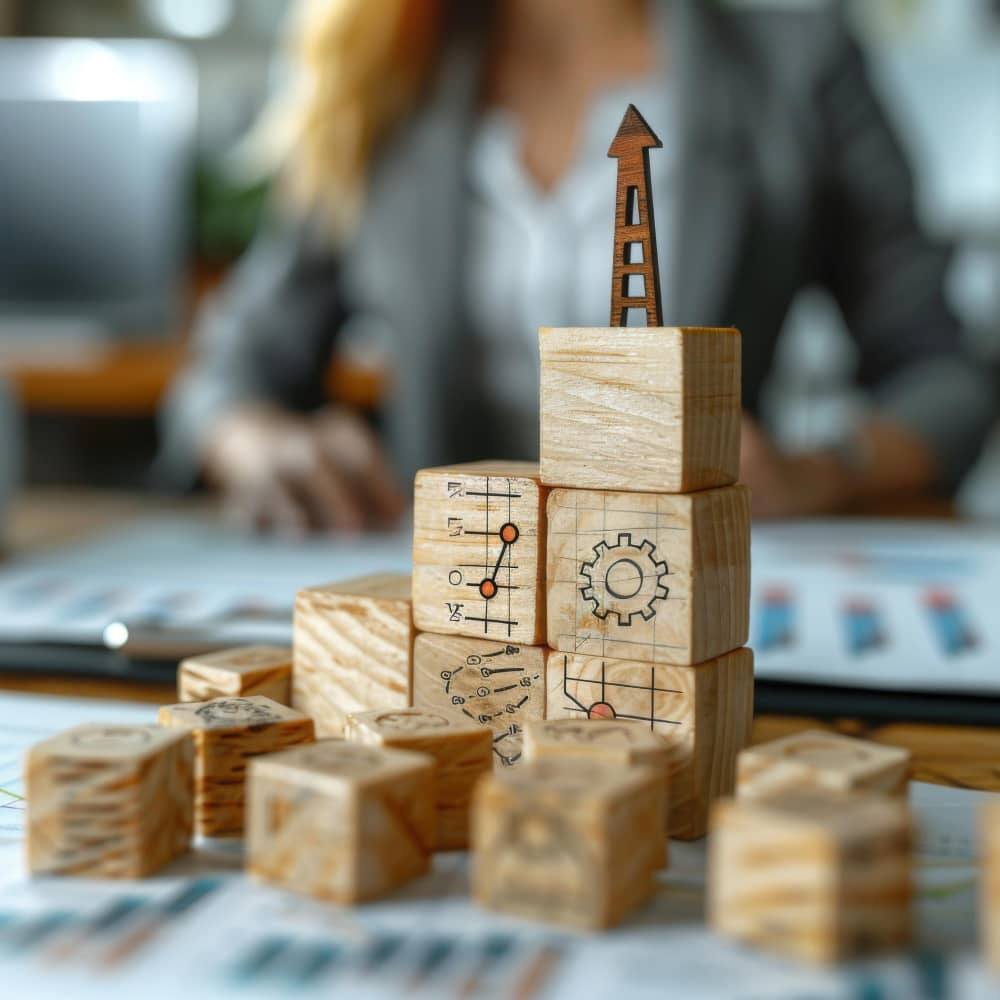
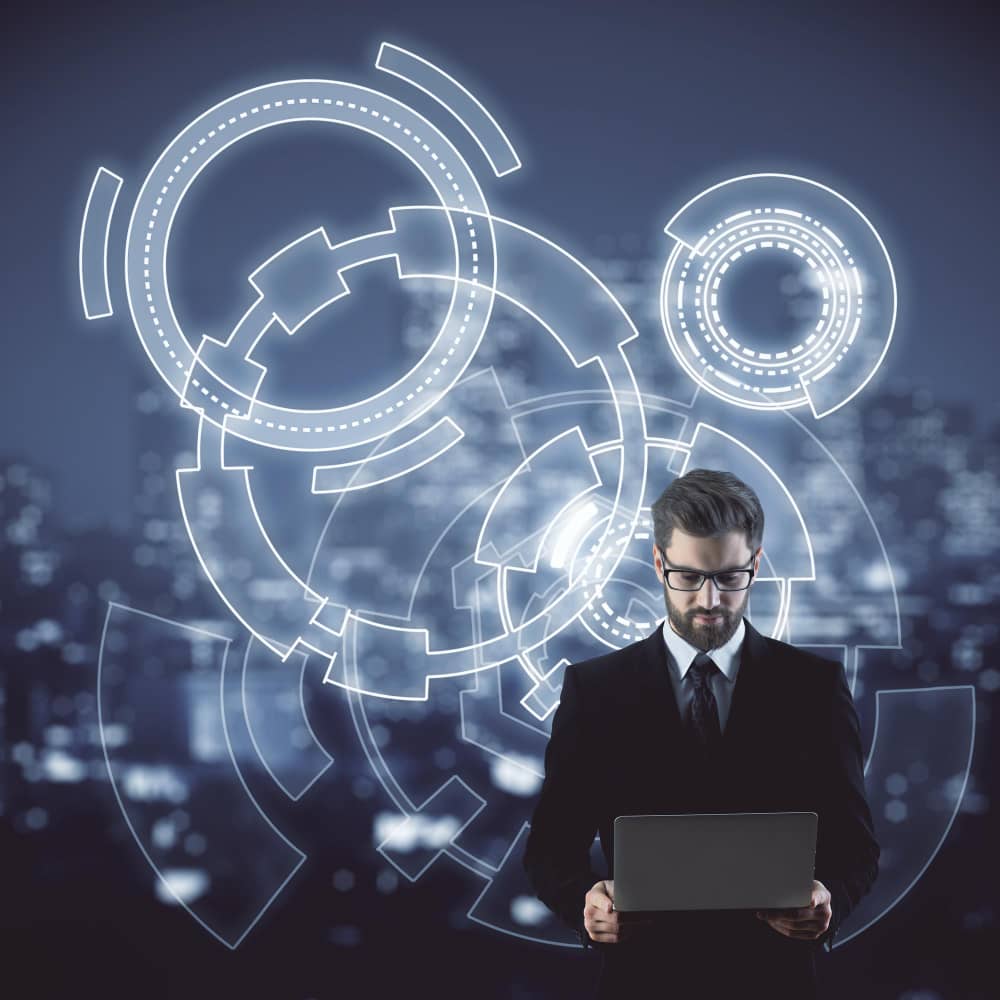
General Characteristics
- Parametric Infrastructure
- Flexible Control and Approval Logic
- Password and Authorization Management System
- Multiple workplace support
- Workflow approach supported by e-mail
- Flexible Reporting and Graphics
- Adaptive Warning Mechanism
- Ability to easily introduce Job/Title changes
- Delegation of authority on leave
- Easy document transfer during the first transition to the system
- Web-based structure
- .NET architecture
- Access via Internet Explorer
- Active Directory Integration
- SQL Server database support
- Ability to work with all SMTP / POP3 compatible mail systems (Notes, Outlook, Exchange, etc.)
BSOFTtpm Modules
BSOFTtpm includes the following modules. And you can use these application modules integrated with each other or independently.
- General Parameter and Definition Operations,
- Kobetsu Kaizen Processes,
- Autonomous Maintenance Operations,
- 5S Operations,
- Education Operations,
- OEE Production Details Operations.
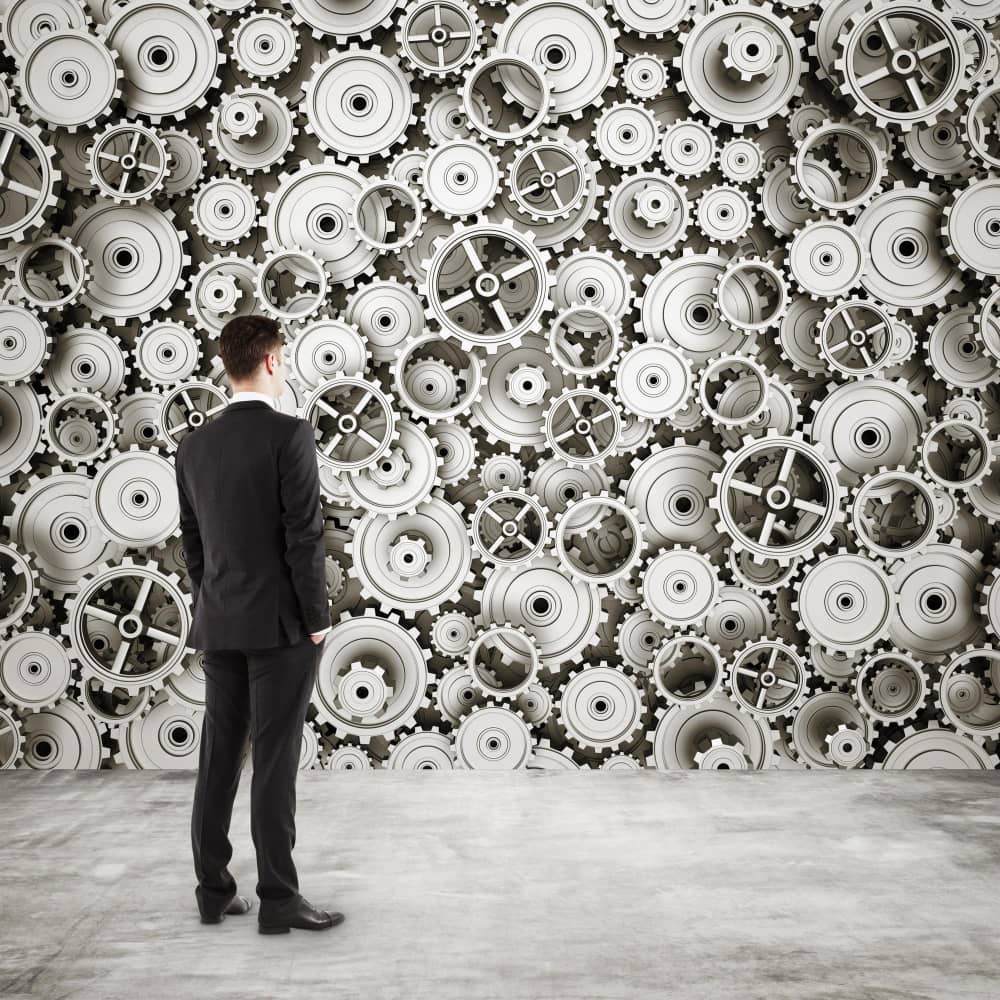
Total Productive Management (TPM)
and Development Process
In order for our industrial organizations to be successful in both national and international markets by increasing their competitiveness, they need to develop completely and rapidly. This development starts from the factory floor and requires the use of an effective methodology for rapid development. In addition to the management style, the use of methods such as Total Productive Management (TPM) and the encouragement of creativity and participation of all employees in the development of products, production processes, quality, thus contributing to competitiveness and company profitability.
TPM is a maintenance approach that requires the participation of all employees in daily production activities, foresees autonomous maintenance, prevents failures, and maximizes equipment efficiency. In other words, TPM is a methodology used to have strong production capability, reduce losses and increase productivity. TPM is a management system that covers all employees in a factory and is mainly based on production efficiency. Many businesses are implementing different systems to reduce costs and increase productivity in competitive market conditions.
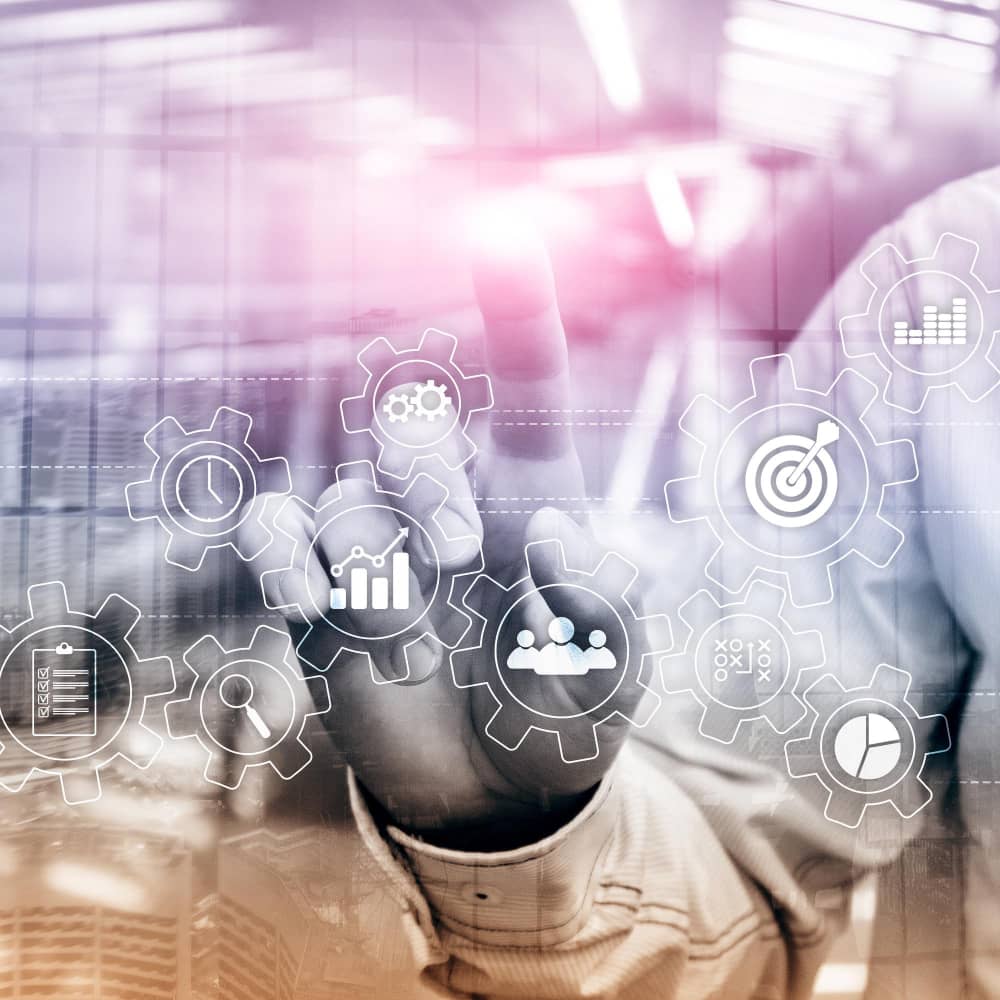
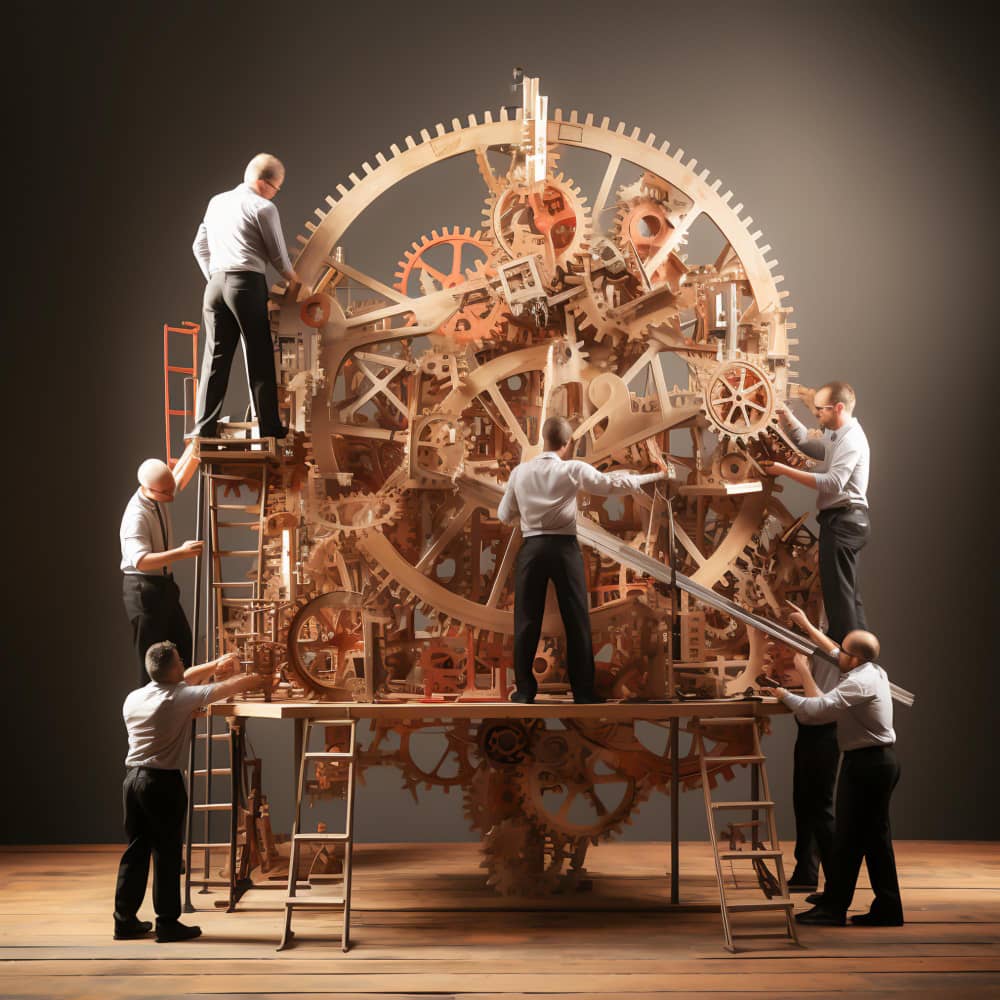
TPM Practices and Improvement Processes
“TPM” is one of the most popular concepts among the practices for factory efficiency. Considering that factories generally employ 7-15 times as many blue-collar employees as management staff, it is an indisputable fact that the continuous improvement of the way of doing business (method) and/or the product by blue-collar employees, who are intertwined with products and production methods every day, every moment, will have a great impact on total improvement.
Managers, teams and employees who have received TPM trainings, become aware and apply the methodology are not satisfied with the existing conditions and standards already achieved, they seek innovations, they are proud of the improvements made and thus communication and loyalty in the factory increases. For this reason, it is essential that activities are recognized. The start for improvements is to recognize the need for improvement. The need arises from recognizing a problem or an inadequate standard. The people who should recognize these problems are those who do the work. If there is no recognized problem, there is no need for improvement, so it is difficult to create an atmosphere suitable for TPM activities.
Implementation of the TPM methodology is very effective in terms of increased individual creativity, especially in blue-collar employees, cooperation of production and office employees to increase efficiency and prevent waste, teamwork, and the formation of an educated and conscious workforce. The continuous generation and accumulation of these benefits translates into an increase in factory efficiency, an increase in product quality, an increase in delivery speed, an efficient management system in total, and a contribution to company profitability.
Feature of TPM Methodology
- Economic efficiency
Creates a company culture that maximizes production system efficiency.
- Total system
It establishes a flawless system that prevents losses related to existing equipment and production area and achieves the 5 “zero” targets (accident, malfunction, minor downtime, error, scrap).
- TPM is a group effort, involving all units and all individuals of the organization.
It is applied by all departments in the enterprise. It is realized with the participation of everyone from the highest level to the lowest level.
- TPM is based on small group activities.
Achieves “zero loss” target with Autonomous Maintenance activities and Kaizen activities.
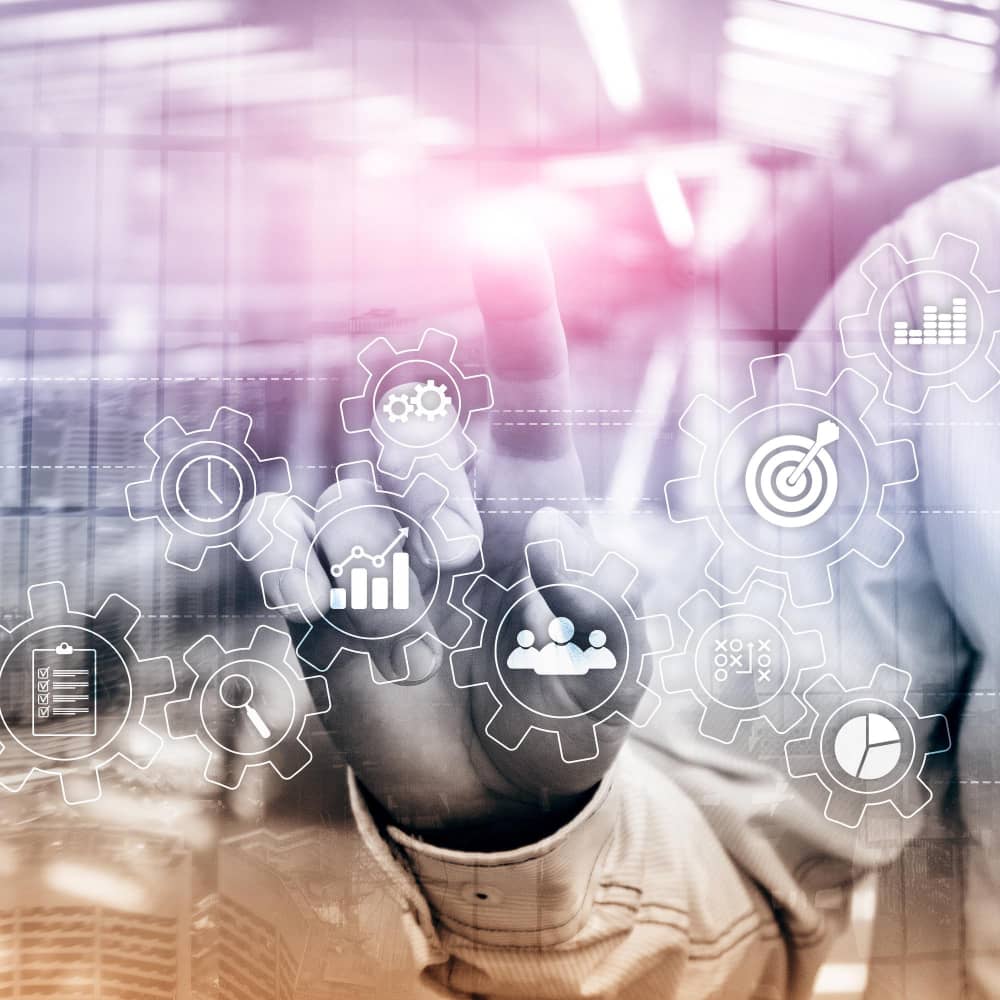
The main objectives of TPM practices;
- To establish a business culture and management system that will maximize the efficiency and effectiveness of the production system together with factory employees and office employees,
- To increase the efficiency of the total equipment, i.e. the entire factory, by collecting the improvements obtained from individual and team work, aiming for a perfect system that will prevent any loss related to the existing equipment and production area,
- To increase the ultimate efficiency (OEE) in maintaining machines and systems by reducing the 16 major losses in the business and to ensure the active participation of all employees in this regard,
8 losses affecting equipment effectiveness:
- Failure
- Set-up adjustment (model change)
- Team change
- Initiation
- Small stop and wait in the gap
- Speed
- Fault and repair
- Shutdown
- 5 losses affecting workforce effectiveness:
- Management
- Production movement
- Line organization
- Logistics
- Measurement and adjustment
- 3 losses affecting material and energy efficiency:
- Energy
- Product
- Equipment( molds and hand tools)
- Ensure consistency in product quality,
- Increased efficiency, reduced losses, accelerated delivery process and increased profitability,
- To ensure occupational safety by improving the working environment and to ensure the formation of a Total Productive Management system that covers all of these, to make it self-sustaining (autonomous) and to continuously improve it.
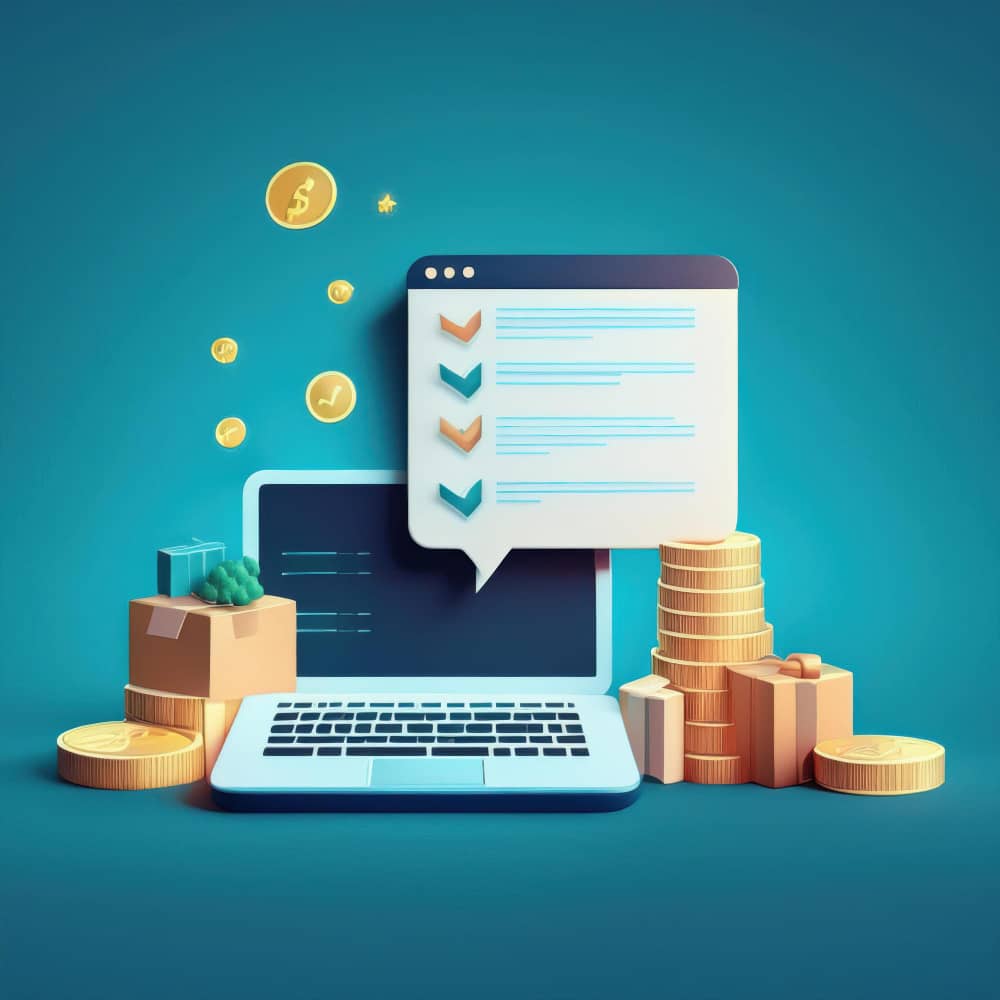
TPM Building Blocks
The following 8 topics in the TPM implementation model constitute the basic building blocks of TPM. A successful TPM implementation is realized by bringing these building blocks together in a correct and healthy way, just like the construction of a house. These building blocks are;
- Kobetsu Kaizen
- Autonomous Maintenance
- Planned Maintenance
- Education
- Early Product/Equipment Management
- Quality Care
- TPM in Office/Management Units
- Occupational Safety, Occupational Health and Environment
As a result, TPM creates a company that
- Capable of producing attractive products with its very high reliability production system,
- Equipped with modern production and information technologies, it has very high productivity,
- Very high competitiveness with low-cost processes,
- Renewed and revitalized with continuous TPM practices, it will be able to meet all kinds of needs,
- Environment, community and employee friendly…
Documents
Modules
Kobetsu Kaizen Operations
Continuous improvement (Kaizen) is a fundamental concept that drives good management. It brings together management philosophies, theories and tools that have been developed and used over the years into a single concept. Continuous improvement is based on continuous, small improvements in the process, especially by workers. Continuous improvement prioritizes the process, it is a management system that supports people’s efforts towards the process. No process, no flow is so perfect that it cannot be improved slightly. The search for opportunities for improvement is everyone’s job, especially those who work on the job.
Wherever and whenever there is an improvement, it will ultimately lead to an improvement in quality and efficiency. Quality is everything that can be improved. Today, when highly competitive businesses are examined, it is seen that the Total Quality phenomenon is underlying their success. The adoption and adaptation of the concept of Kaizen (continuous improvement) as the basic element of Total Quality Management is gaining importance.
Kaizen aims to improve the current situation in small but continuous steps. KAIZEN means “Continuous Improvement”. It is the work done to eliminate 16 major losses to ensure equipment, labor, material and energy efficiency. It also encompasses efforts to improve organization, order, occupational safety and environmental negativities.
Two types of Kaizen are intensively practiced in enterprises. Kaizens differ according to the subject, duration and the path followed:
- Kaizen (Before-After)
- Kobetsu-Kaizen
- Before-After Kaizen
- They are individual-first studies.
- The maximum number of teams can consist of 2 people.
- It comes from experience and common sense.
- It applies at any time.
- It is applied in all areas.
- These are works completed in a short time.
- Kobetsu-Kaizen
- Team-first work.
- The team can consist of a maximum of 5 and a minimum of 3 people.
- It involves 16 major losses.
- Requires data tracking.
- It requires observation and monitoring before and after.
- It can only be applied in its own field.
- They are long-term (min.3-max.6 months) studies.
8 Big Losses Affecting Equipment
- Failure Losses
- Setup Setting Losses
- Team Change
- Initial Losses
- Small Stances
- Speed Losses
- Defective Production and Repair Losses
- Closure Losses
5 Big Losses Affecting the Workforce
- Management Losses
- Production Movement Losses
- Line Organization Losses
- Logistics Losses
- Measurement and Adjustment Losses
3 Major Losses in Material and Energy Efficiency
- Energy Losses
- Jig, Mold and Hand Tool Losses
- Product Losses
For this purpose, BİLTAŞ developed BSOFTtpm Kobetsu Kaizen Transactions, which solves the Kaizen Transactions needs of organizations by transforming Kaizen transactions, one of the cornerstones of TPM in organizations implementing the Total Productive Management System, into an integrated system in the information processing environment.
BSOFTtpm Kobetsu Kaizen Operations is a 100% web-based management module where Kobetsu Kaizen Operations, one of the eight basic building blocks of the Total Productive Management System, can be followed in detail and visually and analysis reports on the results can be created.
Features
- The application is developed with Microsoft . NET technology and is fully object-oriented.
- It has an extremely easy to learn and use user interface.
- The system is designed with a parametric structure.
- Mission-Vision definitions.
- Kaizen related objectives.
- Committee Member procedures.
- Suggestion Card Operations.
- Kaizen processes.
- Poke Yoke operations.
- First then kaizen processes.
- You can design and print unlimited number of reports.
Autonomous Maintenance Operations
Autonomous Maintenance is an activity in which each worker performs cleaning, inspection, lubrication, part replacement (insert, filter element, etc.), simple repair (such as tightening a hose clamp), troubleshooting, accuracy checking and similar activities for their own equipment, aiming to “maintain the proper conditions of their own equipment”.
The idea that the employee voluntarily maintains his/her own machine and even takes part in improvements is the basis of the “maintain your own equipment” view of TPM
In order for Autonomous Maintenance to be carried out at a satisfactory level and for some maintenance responsibilities to be delegated to operators, we need to train them to become people who “understand their machines”. From now on, production staff will have to act not only as operators but also as maintenance workers. The equipment used in factories is increasingly becoming unsupervised, automated machines. Therefore, operators will have more time to take care of their machines.
Autonomous care is implemented in 7 steps and is a team effort.
- Daily cleaning of the machine and learning the signs of problems
- Learning methods to prevent pollution, making hard-to-reach places easily accessible
- Establishment of initial cleaning, inspection and lubrication standards
- General training on control procedures
- Start of “autonomous” controls
- Implementation of Standards and Visual Management
- Start of Fully Autonomous Care
BSOFTtpm Autonomous Maintenance Operations is a web-based application developed to ensure practical, fast and reliable monitoring of autonomous maintenance operations, one of the cornerstones of TPM, and to generate various reports.
Features
- The application is developed with Microsoft . NET technology and is fully object-oriented.
- It has an extremely easy to learn and use user interface.
- The system is designed with a parametric structure.
- You can design and print unlimited number of reports.
Mission Vision
The actions to be taken in relation to autonomous maintenance and the way in which they are carried out are defined. These are renewed when necessary.
Target
Goals related to autonomous care are set. These targets are used for step skipping, etc. (How many suggestion cards to post, or how many negativity cards to post, etc.) Targets are necessary for the distribution of points if achieved and for the transition to the next steps.
Committee Members
Selection of the personnel who will assign and evaluate the autonomous maintenance. This staff selects personnel to work on various tasks. Establishes and directs the teams. Makes evaluations as a result of the work done.
Deployment Plan
Determining the tasks and deadlines for the assigned groups to achieve their autonomous care goals. The methods to be followed to reach the set targets are determined, and plans that go beyond the deadline are reviewed.
Team Members
Selection of staff to implement and be responsible for the dissemination plan. Personnel are selected by the Committee members based on their training and competencies. When deemed necessary, team members can be changed, added or removed.
Negativity Card Entry
- Reporting of negative situations related to various locations, machines and vehicles, which are detected by the personnel and scored for reward. Negativity cards are printed and hung in the relevant place. These cards can be seen by everyone. Personnel who report negativity receive points for this.
- The personnel who resolved the negativity removes this card and reports how they resolved the negativity. They indicate when and what they did to eliminate the negativity.
- Committee Members review and evaluate the removed negativity cards. If necessary, they cancel the improvement and reactivate the card.
- Those who make improvements due to approved cards earn points
Meeting Decisions
- At meetings held at various times, the participants are determined and the decisions taken at the meeting are recorded.
- The meeting time, subject and participants are determined.
- Staff not attending the meeting will be dismissed.
- Decisions taken at the end of the meeting are recorded.
Pollution Sources
- The location, machinery and vehicles causing pollution are identified and graded.
- Minimum values for pollution are determined.
- Identify existing pollution and determine the level at which this pollution can be reduced
- The value to be achieved and the time to achieve this value are defined.
Step Jump Supervision
- Supervision of the successful implementation of the dissemination plan. Evaluation of the success points in the specified conditions.
- The items to be evaluated for the dissemination plan are identified. These items can be categorized under various groups.
- Each of these items is awarded points in proportion to the success in implementing the dissemination plan.
- These scores are summed up to determine whether the step jump is performed according to the set target.
- If a step change has occurred, a new roll-out plan is prepared or an existing one is handed over to the team.
Hard to Access, Control and Maintain Areas.
- Places that are difficult to control and maintain within the enterprise are identified.
- Related documents (photographs, etc.) are collected.
- The reasons for difficult maintenance and control are identified.
- Attempts are made to eliminate the identified causes, which are then rechecked and documented
Sharing Responsibility
- Responsible and department assignments are made to the plans made for the determined autonomous maintenance operations.
- The responsible and the department are selected from departments related to autonomous care.
- The work to be done and the plan are determined and the time required for the realization of this plan is notified.
Near Miss
- Situations that may cause work accidents are determined. The determined situation is documented by hanging a card in the relevant place.
- The work accident group is identified and the conditions that may lead to this work accident are explained in detail.
- Removes personnel card eliminating the risk of accidents.
- The removed card will be evaluated by the committee members, and if it is decided that there is no appropriate solution, the card will be reactivated.
- If the card removal is approved by the committee, the reporting staff and the staff who improve the near-miss will receive points.
5S Operations
The 5S methodology aims to create enterprises that have achieved the targeted gains and have a system open to continuous improvement by raising employee awareness. 5S is a simple and easy-to-implement system that contributes greatly to occupational safety, quality, productivity, machine performance, inventory control, employee participation and motivation. 5S provides employees with pleasant and safe working conditions, makes them feel a sense of “belonging” to the workplace, instills the awareness of “my field, my machine and my factory” and improves teamwork.
The 5S methodology, named after the Japanese initials for the 5 steps that make up the system, is not a magical self-managing system. In order to be effective, everyone in the company must apply this system over and over again. In order to achieve the desired success in implementation and to ensure its continuity, the belief and support of everyone from the top management of the company to the operator level is essential.
5S Steps:
Step 1 Sequence (Recovery-Sorting)
In the sorting step, the site is reviewed in detail and necessary and unnecessary materials, stock materials, fixtures, tools, etc. are separated from each other. These materials are usually kept in case they are needed one day or broken but not disposed of.
These unnecessary materials are collected in an area and evaluated. The first thing to do is to ensure that all relevant departments are aware of these materials and give them to the departments that need them. The remaining materials are sold as scrap, donated, etc. They are disposed of through sorting methods. This step is like the foundation of the building and should be implemented as strictly as possible.
Step 2 SEITON (Layout)
The organization step is the step of addressing all materials, fixtures, tools, etc. that are constantly needed. The aim should be to reach all the materials needed as soon as possible and to make it easy to pick up and drop off. In this step, all these materials are arranged, placed and marked in the closest way to the work area, taking into account ergonomics and occupational safety, and the order and stock quantities are decided by determining the minimum and maximum stock levels.
Step 3 SEISO (Cleaning)
The aim of the cleaning step is to remove all dust and dirt from the work area and keep it spotless. Employees should be responsible for cleaning their own areas, but they cannot spend most of their time cleaning. In this step, the employee who knows his/her site identifies all sources of pollution and seeks improvement through kaizens.
Each department and area has a responsible person. Various cleaning methods are developed and standardized.
Step 4 SEIKETSU (Standardization)
This step is the standards, improvements and control methods to be established to ensure the continuity of the achievements (studies) obtained in the first three steps and to maintain this positive situation reflected on the field. It has three main objectives;
- Zero Confusion
- Zero unnecessary parts
- Zero Pollution
The field identifies the points that need to be questioned and carries out improvement activities, taking into account the above three headings.
Step 5 SHITSUKE (Discipline)
Step 5 is to make adherence to the rules a habit, to develop and maintain activities. Everyone should inspect the work area and equipment at all times and provide the necessary training to each new team member. The workplace should now be spontaneously activated.
Benefits of the discipline step;
- Improves employees’ sense of responsibility
- Employees’ self-confidence increases
- The roles of the employee are defined
- The employee makes his/her presence felt
- No loss of activity as there are no flashbacks
- Increased employee motivation
BSOFTtpm 5S Operations is a web-based application where committee members are defined, audit questions are created, 5S cards are entered and audit results are analyzed.
Features
- The application is developed with Microsoft . NET technology and is fully object-oriented.
- It has an extremely easy to learn and use user interface.
- The system is designed with a parametric structure.
- You can design and print unlimited number of reports.
OEE Production Detail Operations
OEE (Overall Equipment Effectiveness) is a “best practices” way to monitor and improve the effectiveness of your production processes (e.g. machines, production cells, assembly lines). OEE is simple and practical. It takes the most important and common sources of production efficiency losses, places them into three main categories and decomposes them into metrics. These metrics provide the perfect measurement infrastructure to gauge where you are and how to improve.
OEE is often used as a key metric in TPM (Total Productive Maintenance) and lean manufacturing programs. It provides a consistent way to measure the effectiveness of TPM and other initiatives by providing a common framework for measuring production efficiency. OEE really does turn complex manufacturing problems into simple, understandable information. It allows you to systematically improve your processes with simple measurements.
Six Big Losses
The main objectives of OEE and TMP programs are to reduce or eliminate the “Six Big Losses” (the leading causes of lost productivity in production). The Six Big Losses;
- Malfunctions
- Setup and Adjustments
- Small stops
- Low Speed
- Start Retleri
- Production Rejects
BSOFTtpm Production Details Operations is a web-based application that provides a consistent path to the success of TPM by providing a general framework for measuring production efficiency, turning complex production problems into simple, understandable information and enabling the systematic improvement of processes with simple measurements.
Features
- The application is developed with Microsoft . NET technology and is fully object-oriented.
- It has an extremely easy to learn and use user interface.
- The system is designed with a parametric structure.
- You can design and print unlimited number of reports.
OEE Cycle Times
It is determined how long it takes to produce the product on the specified line. Products can be produced in different times in each line, in the enterprise
For each line, it is determined how long it takes to produce the product and this value is entered into the system.
Reasons for stopping
The reasons for stoppages during production are determined. Some of these stoppages are included in OEE and some are not used in OEE calculation.
The reasons for stoppages can be machine-related such as breakdowns, maintenance, configuration or even raw material shortages due to unavailable reasons (power outage, etc.) or poorly planned work.
The missing rate after all necessary stops can be used to determine performance.
Production Reports
- The products produced during the working period and the downtimes during this period are entered. With these inputs, the OEE percentage is determined, if desired and if production and downtime are entered frequently enough, real-time OEE can be monitored.
- At the end of the period, it is calculated how productive this working time was. This is a rough calculation, the percentage is calculated by including and excluding downtimes.
- At the end of the study, a detailed production report is produced. This report shows how much of which product was produced, how many defective products were produced and how many products can be repaired and reused. This report can be changed flexibly according to different situations.
Production Indicators
- These are dials that show OEE percentage in various ways according to date, line and shift.
- In this way, the manager can visually see the instantaneous productivity in the business at any time, as well as the status of various units in the past.
Start Your Digital Transformation Journey with Biltaş
Meet smart software solutions that will optimize your business processes and increase your productivity.