TPM Toplam Verimlilik Yönetimi
BSOFTtpm ile Toplam Verimlilik Yönetimini Uygulayarak Verimliliği Artırın
Toplam Verimlilik Yönetimi (TPM) ve BSOFTtpm Çözümleri
Sanayi kuruluşlarımızın rekabet güçlerini artırarak gerek ulusal, gerekse uluslararası pazarlarda başarılı olabilmeleri için topyekün ve hızlı gelişmeleri gereklidir. Bu gelişmeler fabrika sahasından başlar ve hızlı gelişim için etkin bir metodolojinin kullanımı gereklidir.
Gelişmede yönetim tarzının yanısıra, Toplam Üretken Yönetim (TPM) gibi metodların kullanımı ile tüm çalışanların yaratıcılıklarının teşviki, katılımları ile doğan iyileşmelerin ürünlere, üretim süreçlerine, kaliteye, dolayısı ile rekabet gücü ve firma karlılığında katkısı büyüktür.
TPM, günlük üretim faaliyetlerin içerisinde, çalışanların tamamının katılımını gerektiren, otonom bakımı öngören, arızaları önleyen, ekipman etkinliğini en üst düzeye getiren bir bakım yaklaşımıdır. Başka bir deyişle TPM, güçlü üretim yeteneğine sahip olmak, kayıpların azaltılması ve verimliliğin arttırılması için kullanılan bir metodolojidir.
BSOFTtpm, sanayi ve üretim sektörünün Toplam Verimlilik Yönetim (TPM) metodlarının otomasyonunu sağlamak için esnek, parametrik ve modüler yapıya sahip, birbirleriyle entegre çalışan birçok uygulama modülünden oluşan ve microsoft ASP/ASP.NET teknolojisi kullanılarak geliştirilmiş, %100 web tabanlı bir yazılımdır.
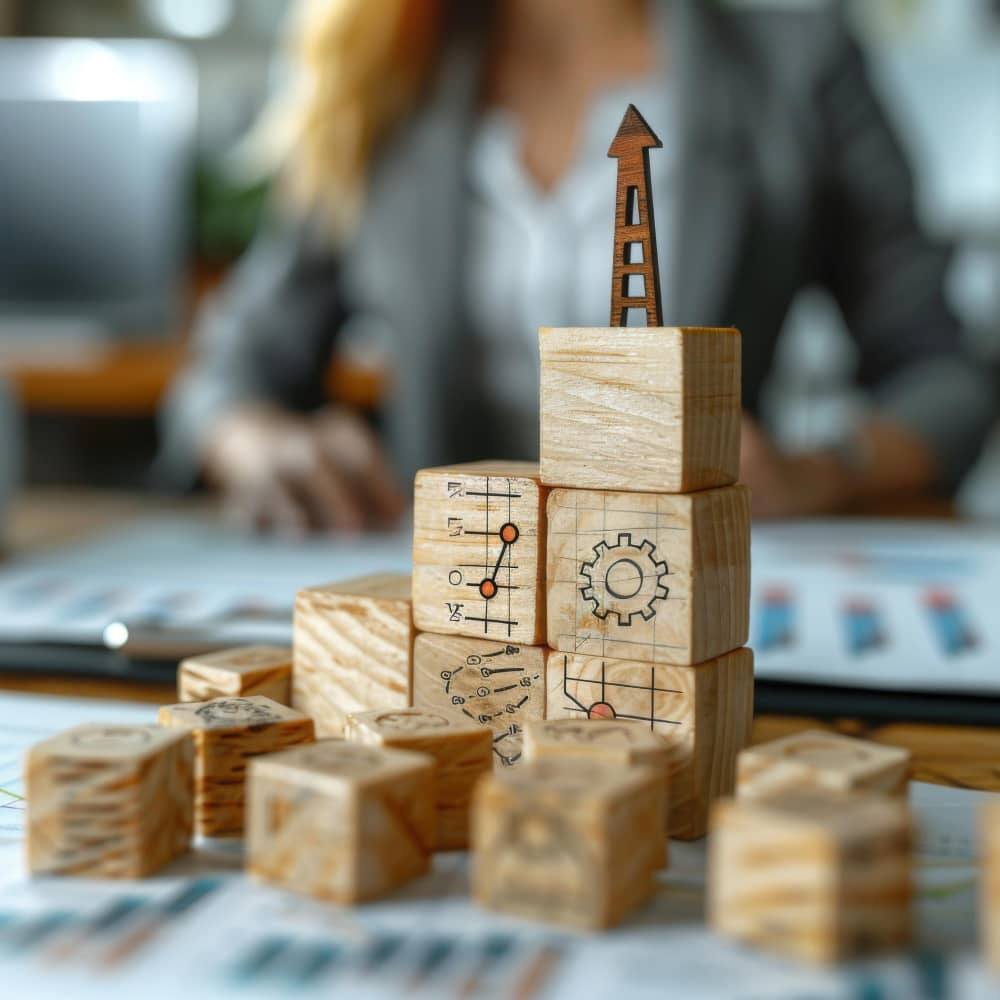
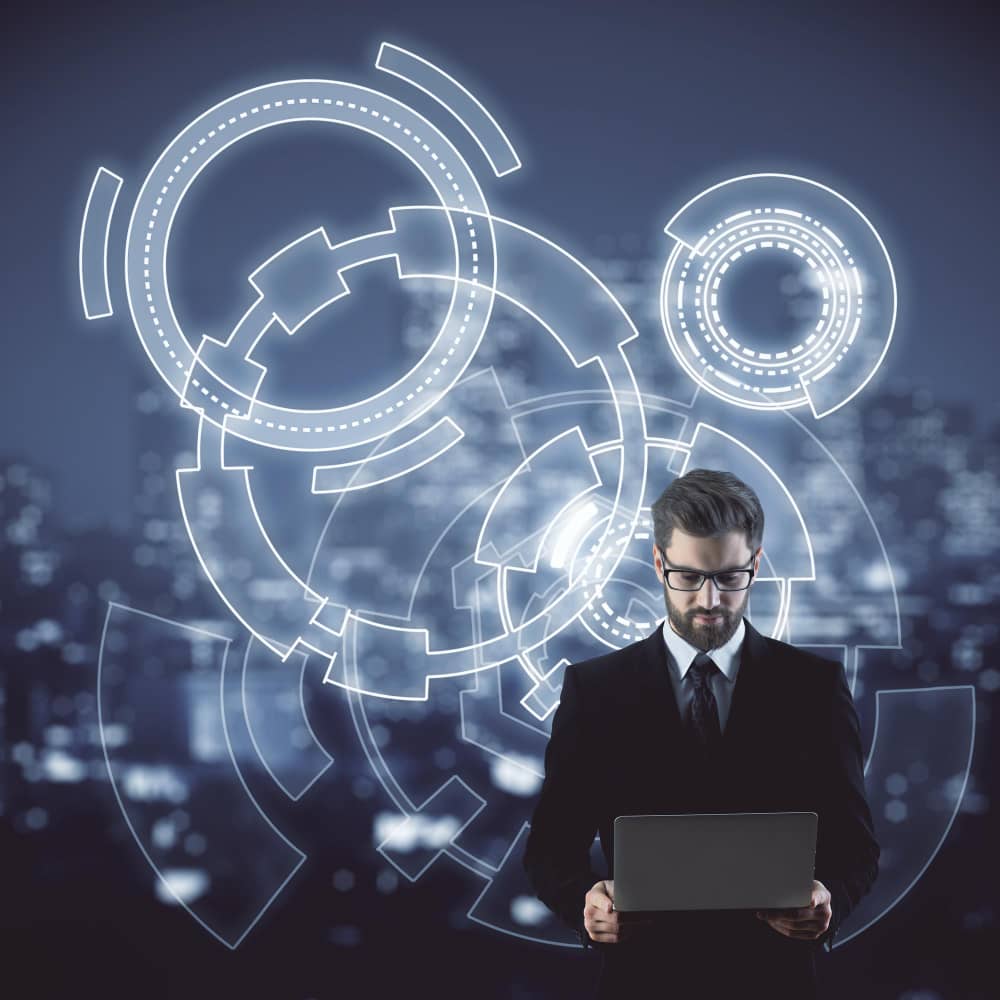
Genel Özellikleri
- Parametrik Altyapı
- Esnek Kontrol ve Onay Mantığı
- Parola ve Yetki Yönetim Sistemi
- Birden fazla işyeri desteği
- E-mail destekli iş akışı (Workflow) yaklaşımı
- Esnek Raporlama ve Grafikler
- Uyarlanabilir Uyarı Mekanizması
- İş / Ünvan değişikliklerini kolayca tanıtabilme
- İzinde yetki delegasyonu
- Sisteme ilk geçişte kolay döküman aktarma
- Web tabanlı yapı
- .NET mimarisi
- Internet Explorer üzerinden erişim
- Active Directory Entegrasyonu
- SQL Server veri tabanı desteği
- Tüm SMTP / POP3 uyumlu mail sistemleri ile çalışabilme (Notes, Outlook, Exchange vb)
BSOFTtpm Modülleri
BSOFTtpm, aşağıdaki modüleri içermektedir. Ve bu uygulama modüllerini birbirleriyle entegre veya bağımsız olarak kullanabilirsiniz.
- Genel Parametre ve Tanımlama İşlemleri,
- Kobetsu Kaizen İşlemleri,
- Otonom Bakım İşlemleri,
- 5S İşlemleri,
- Eğitim İşlemleri,
- OEE Üretim Detayları İşlemleri.
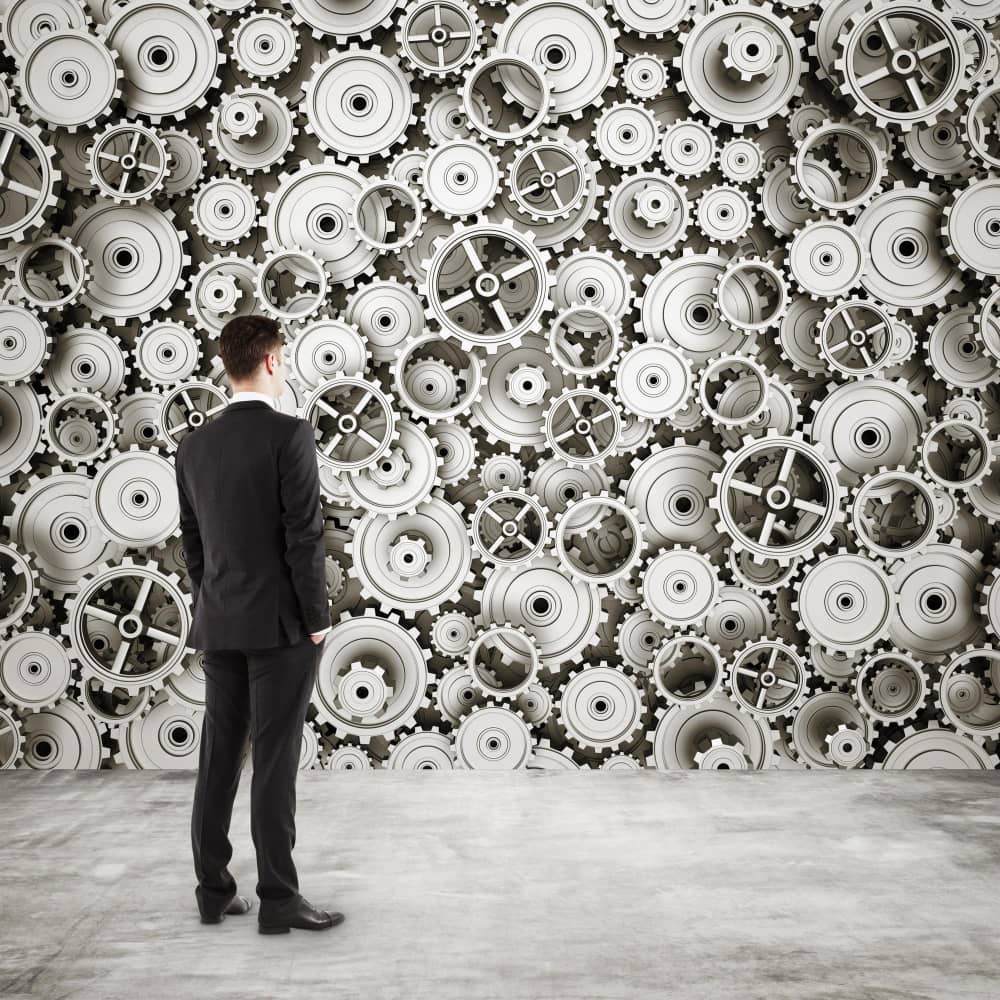
Toplam Üretken Yönetim (TPM)
ve Gelişim Süreci
Sanayi kuruluşlarımızın rekabet güçlerini artırarak gerek ulusal, gerekse uluslararası pazarlarda başarılı olabilmeleri için topyekün ve hızlı gelişmeleri gereklidir. Bu gelişmeler fabrika sahasından başlar ve hızlı gelişim için etkin bir metodolojinin kullanımı gereklidir. Gelişmede yönetim tarzının yanısıra, Toplam Üretken Yönetim (TPM) gibi metodların kullanımı ile tüm çalışanların yaratıcılıklarının teşviki, katılımları ile doğan iyileşmelerin ürünlere, üretim süreçlerine, kaliteye, dolayısı ile rekabet gücü ve firma karlılığında katkısı büyüktür.
TPM, günlük üretim faaliyetlerin içerisinde, çalışanların tamamının katılımını gerektiren, otonom bakımı öngören, arızaları önleyen, ekipman etkinliğini en üst düzeye getiren bir bakım yaklaşımıdır. Başka bir deyişle TPM, güçlü üretim yeteneğine sahip olmak, kayıpların azaltılması ve verimliliğin arttırılması için kullanılan bir metodolojidir. TPM bir fabrikadaki tüm çalışanları kapsayan ve ağırlıklı olarak üretim verimini esas alan bir yönetim sistemidir. Birçok işletme, rekabetçi piyasa koşullarında maliyetlerin azaltılması ve verimliliğin artırılmasına yönelik değişik sistemler uygulamaktadır.
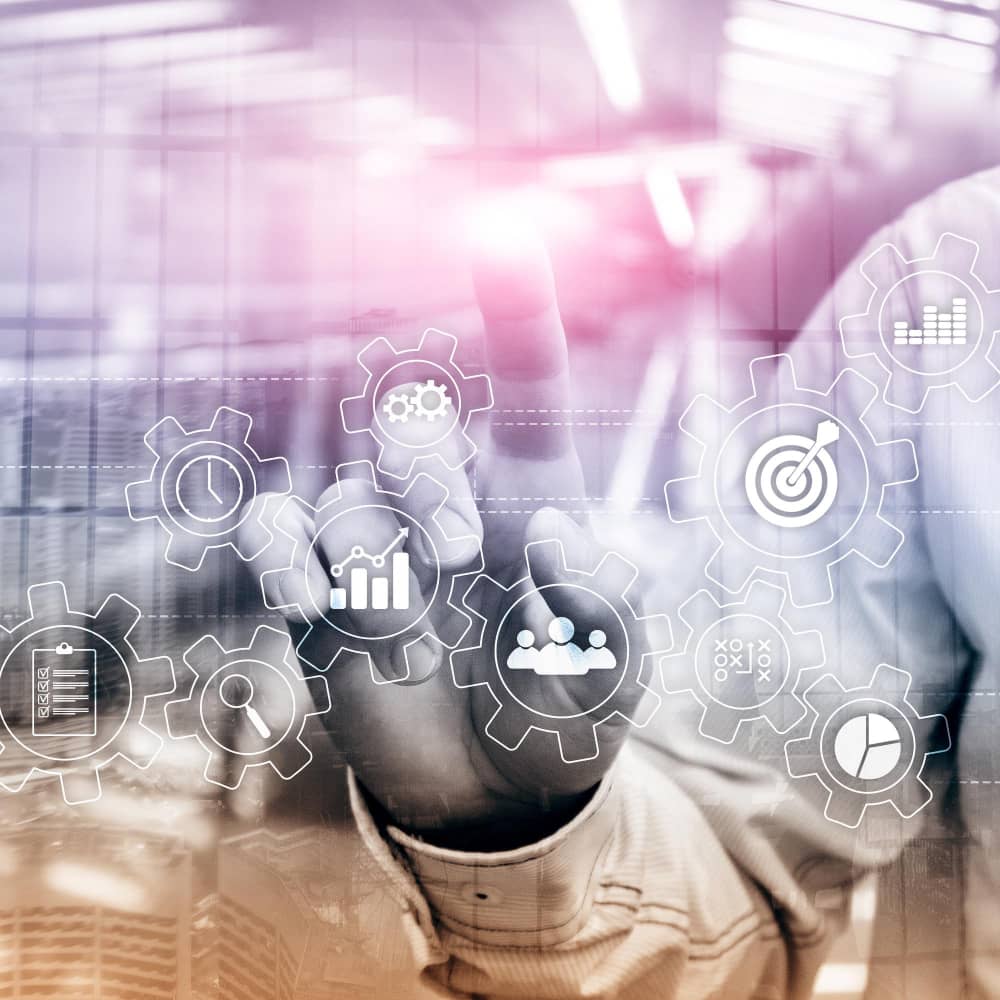
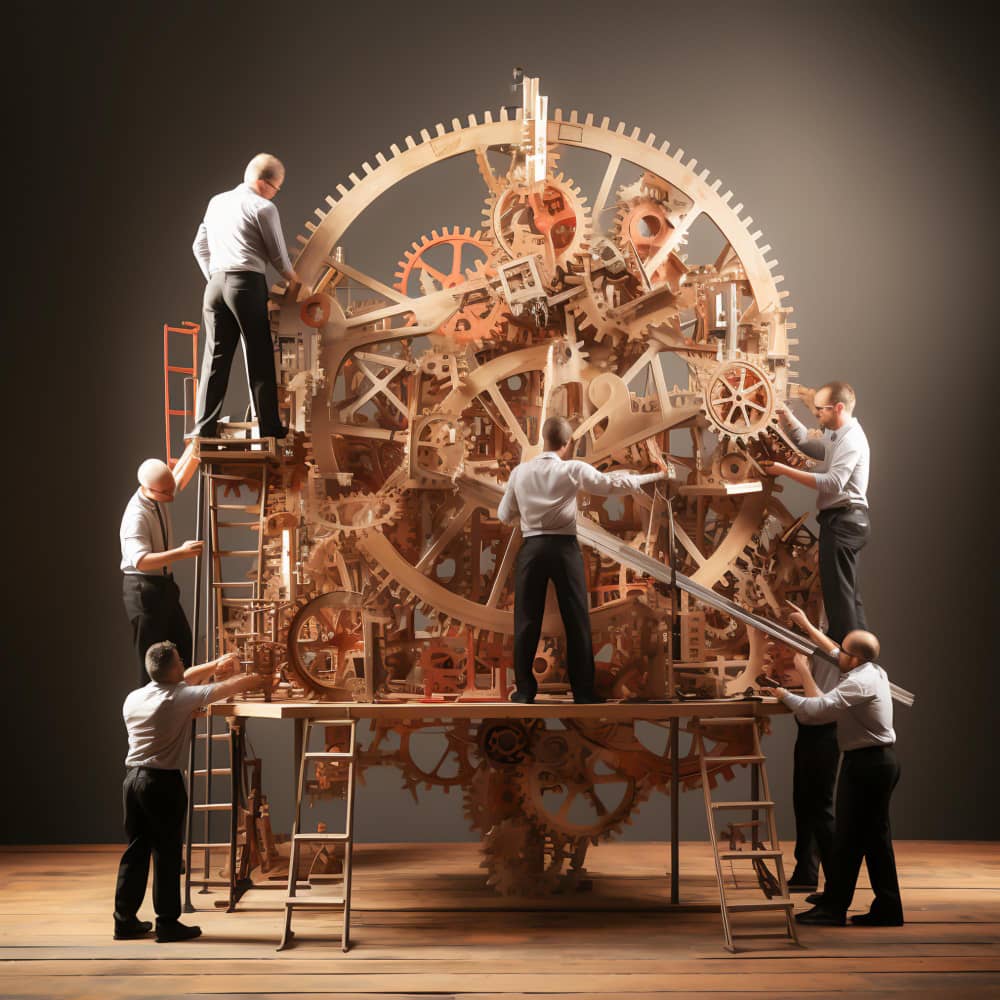
TPM Uygulamaları ve İyileştirme Süreçleri
Fabrika verimine yönelik uygulamaların içinde adı çok duyulan bir kavram da “TPM”dir. Genelde fabrikalarda yönetim kadrosunun 7-15 misli mavi yakalı personel çalıştığı düşünülürse, her gün, her an ürünler ve üretim metotları ile iç içe olan mavi yakalı çalışanların iş yapış tarzını (metodu) ve/veya ürünü sürekli iyileştirmesinin toplam iyileşmeye büyük etkisi olacağı tartışılamaz bir gerçektir.
TPM eğitimleri almış, bilinçlenmiş ve metodolojiyi uygulayan yöneticiler, ekipler ve çalışanlar mevcut koşullarla, zaten ulaşılmış olan standartlar ile yetinmez, yenilikler arar, yapılan iyileştirmelerle gurur duyarlar ve bu sayede fabrikada iletişim ve bağlılık artar. Bu nedenle yapılan faaliyetlerin takdir edilmesi şarttır. İyileştirmeler için başlangıç, iyileştirmeye olan ihtiyacın fark edilmesidir. İhtiyaç bir problemin ya da yetersiz standardın fark edilmesiyle ortaya çıkar. Bu problemleri fark etmesi gerekenler bizzat işi yapanlardır. Fark edilen bir problem yoksa iyileştirmeye ihtiyaç doğmaz, dolayısı ile TPM aktivitelerine uygun atmosfer zor oluşur.
TPM metodolojisinin uygulanması, özellikle mavi yakalı çalışanlarda artan bireysel yaratıcılık, verim artırarak israfı önlemek amacına yönelik üretim ve ofis çalışanlarının işbirliği, ekip çalışmaları, eğitimli ve bilinçli işgücünün oluşması açısından çok etkindir. Bu getirilerin sürekli fayda üretmesi ve birikmesi fabrika veriminin artışı, ürün kalitesindeki artış, teslimat hızının artışı, toplamda verimli bir yönetim sistemine dönüşmekte, şirket kârlılığına katkı yaratmaktadır.
TPM Metodolojisinin Özelliği
- Ekonomik etkinlik
Üretim sistem etkinliğini maksimize edecek şekilde bir şirket kültürü oluşturur.
- Toplam sistem
Mevcut ekipman ve üretim alanı ile ilgili kayıpları önleyen ve 5 “sıfır” (kaza, arıza, küçük duruş, hata, hurda) hedefine ulasacak kusursuz bir sistem kurar.
- TPM grup çalışmasıdır, organizasyonun tüm birimlerini ve tüm bireylerini içerir.
İşletmede bulunan tüm departmanlar tarafından uygulanır. En yüksek kademeden en alt kademeye kadar herkesin katılımı ile gerçekleştirilir.
- TPM küçük grup aktivitelerine dayanır.
Otonom Bakım faaliyetleri ve Kaizen aktiviteleri ile “sıfır kayıp” hedefine ulaşır.
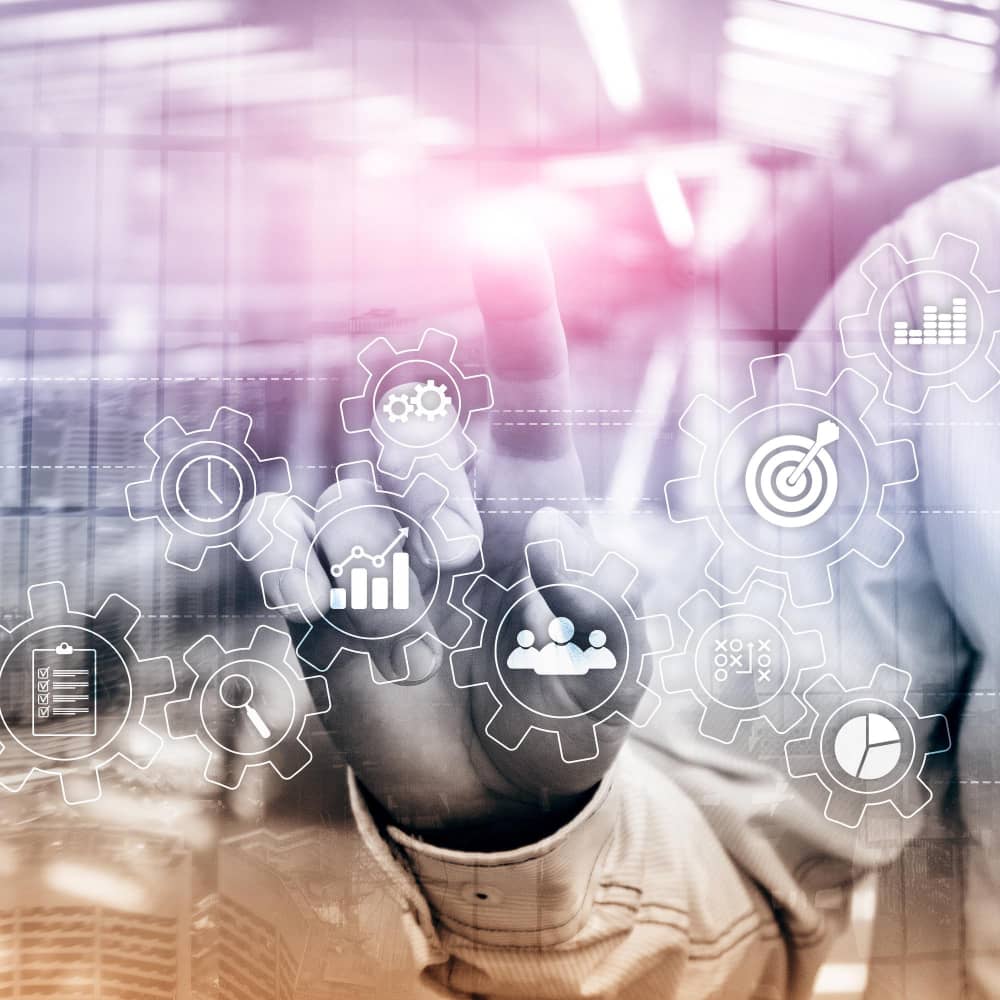
TPM uygulamalarının başlıca amaçları;
- Üretim sisteminin verim ve etkinliğini en üst düzeye çıkaracak bir işletme kültürü ve yönetim sistemini fabrika çalışanları, ofis çalışanları ile beraber yerleştirmek,
- Mevcut ekipman ve üretim alanı ile ilgili her türlü kaybı önleyecek kusursuz bir sistem amaçlayarak, bireysel ve ekip halinde çalışmalardan elde edilen iyileşmelerin toplanması ile toplam ekipmanların yani tüm fabrikanın verimini arttırmak,
- İşletmede ortay çıkan 16 büyük kayıbı azaltarak; makina ve sistemlere bakım yapmaya nihai verimi (OEE) arttırmak ve buna yönelik tüm çalışanların aktif katılımını sağlamak,
Ekipman etkinliğini etkileyen 8 kayıp:
- Arıza
- Set-up ayar ( model değisimi)
- Takım değisimi
- Baslangıc
- Kucuk durus ve bosta bekleme
- Hız
- Hata ve tamir
- Kapatma
- İş gücü etkinliğini etkileyen 5 kayıp:
- Yonetim
- Uretim hareket
- Hat organizasyon
- Lojistik
- Olcme ve ayar
- Malzeme ve enerji etkinliğini etkileyen 3 kayıp:
- Enerji
- Urun
- Ekipman( kalıp ve el aletleri)
- Ürün kalitesinde istikrar sağlamak,
- Artan verim, azalan kayıplar, hızlanan teslimat süreci ile kârlılığı artırmak,
- Çalışma ortamını iyileştirerek iş güvenliği sağlamak ve bunların hepsini kapsayan Toplam Verimli Yönetim sisteminin oluşmasını sağlayarak kendi kendine yürür (Otonom) hale getirmek, sürekli geliştirmektir.
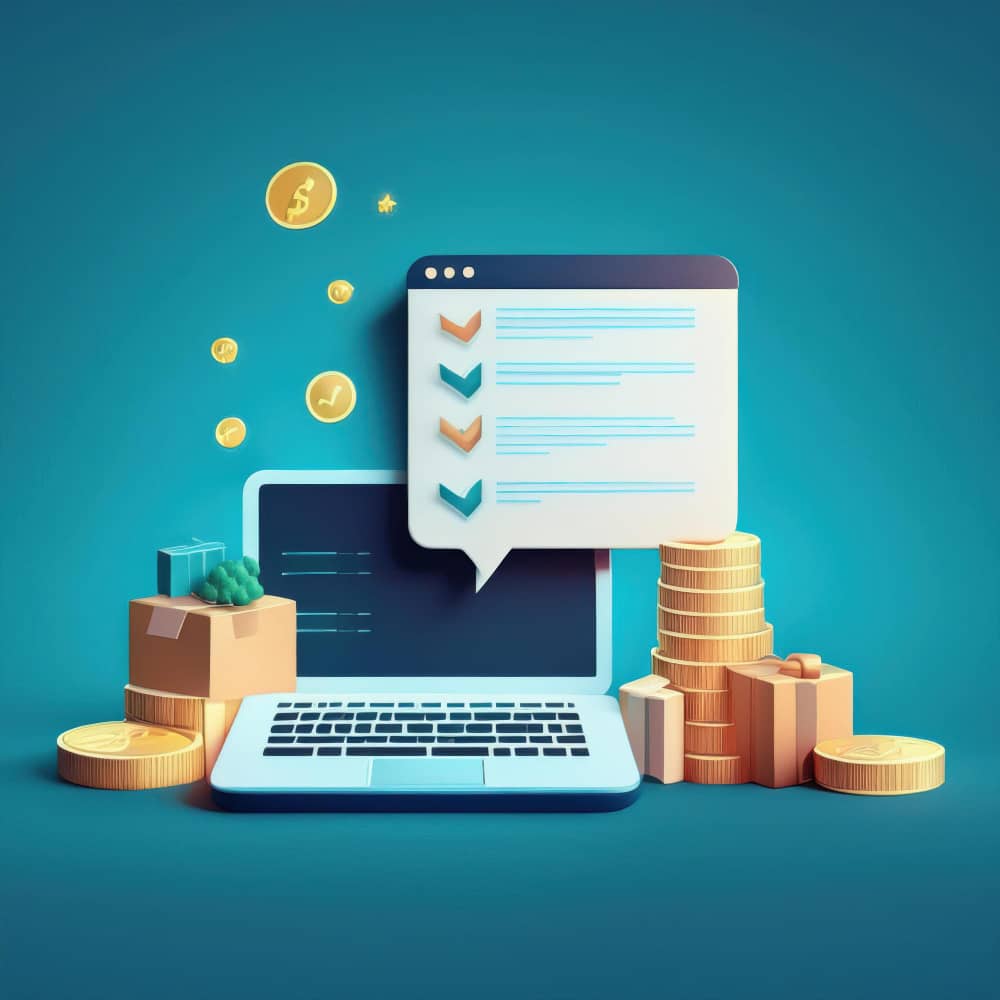
TPM Yapı Taşları
TPM uygulama modelinde aşağıda yer alan 8 konu, TPM’in temel yapı taşlarını oluşturmaktadır. Başarılı bir TPM uygulaması, tıpkı bir evin inşaası gibi bu yapı taşlarının doğru bir şekilde ve sağlıklı olarak yan yana getirilmesi ile gerçekleştirilir. Bu yapı taşları;
- Kobetsu Kaizen
- Otonom Bakım
- Planlı Bakım
- Eğitim
- Erken Ürün/Ekipman Yönetimi
- Kalite Bakımı
- Ofis/Yönetim Birimlerinde TPM
- İş Güvenliği, İş Sağlığı ve Çevre
Sonuç olarak TPM, aşağıdaki özellikleri sağlayan bir şirket yaratır.
- Sahip olduğu çok yüksek güvenilirlikli üretim sistemi ile çekici ürünler üretebilen,
- Modern üretim ve bilişim teknolojileri ile donatılmış, üretkenliği çok yüksek,
- Düşük maliyetli süreçlere sahip, çok yüksek rekabet yeteneği olan,
- Sürekli TPM uygulamaları ile yenilenmiş, yeniden canlandırılmış, her türlü ihtiyacı karşılayabilecek,
- Çevre, toplum ve çalışan dostu..
Dökümanlar
Modüller
Kobetsu Kaizen İşlemleri
Sürekli iyileştirme (Kaizen), iyi yönetimi yönlendiren temel bir kavramdır. Yıllar içinde geliştirilmiş ve kullanılmış yönetim felsefelerini, teorilerini ve araçlarını bir araya getirmiş tek bir kavram altında toplamıştır. Sürekli iyileştirmenin temelinde; proseste özellikle işçiler tarafından gerçekleştirilen sürekli, küçük iyileştirmeler yatar. Sürekli iyileştirme prosese öncelik verir, kişilerin prosese yönelik çabalarını destekleyen bir yönetim sistemidir. Hiç bir işlem, hiç bir akış küçük bir iyileştirme yapılamayacak kadar mükemmel değildir. İyileştirme olanaklarının araştırılması herkesin, özellikle de o işte çalışanların görevidir.
Nerede ve ne zaman bir iyileştirme olsa, bu sonuçta kalitede ve verimlilikte bir iyileşmeye yol açacaktır. Kalite, iyileştirilebilen her şeydir. Günümüzde rekabet gücü yüksek işletmeler incelendiğinde bunların başarılarının altında Toplam Kalite olgusunun yer aldığı görülmektedir. Toplam Kalite Yönetimi’nin temel unsuru olarak ta Kaizen (sürekli iyileştirme) kavramının benimsenmesi ve işletme bünyesine adaptasyonu önem kazanmaktadır.
Kaizen küçük, fakat sürekli adımlarla mevcut durumun iyileştirilmesini hedefler. KAIZEN “Sürekli İyilestirme” demektir. Ekipman, işçilik, malzeme ve enerji etkinliğinin sağlanması için 16 büyük kaybın yok edilmesine yönelik yapılan çalışmalardır. Bunun dışında tertip düzen, iş güvenliği ve çevreye yönelik olumsuzlukların iyileştirilmesi çalışmalarını da kapsar.
İşletmelerde yoğun olarak iki çeşit Kaizen uygulanmaktadır. Kaizenler konu, süre ve izlenen yol durumlarına göre farklılık gösterirler:
- Kaizen ( Önce-Sonra )
- Kobetsu-Kaizen
- Önce-Sonra Kaizen
- Birey öncelikli çalışmalardır.
- Ekip sayısı en fazla 2 kişiden oluşabilir.
- Tecrübe ve sağduyu ile gerçekleşir.
- Her an uygulanır.
- Tüm alanlarda uygulanır.
- Kısa sürede tamamlanan çalışmalardır.
- Kobetsu-Kaizen
- Ekip öncelikli çalışmalardır.
- Ekip en fazla 5 en az 3 kişiden oluşabilir.
- 16 büyük kaybı içerir.
- Veri takibi gerektirir.
- Öncesinde ve sonrasında gözlem ve izleme gerektirir.
- Sadece kendi alanı ile ilgili uygulanabilir.
- Uzun süreli ( min.3-max.6 ay) çalışmalardır.
Ekipmanı Etkileyen 8 Büyük Kayıp
- Arıza Kayıpları
- Setup Ayar Kayıpları
- Takım Değisimi
- Başlangıç Kayıpları
- Küçük Duruşlar
- Hız Kayıpları
- Hatalı Üretim ve Tamir Kayıpları
- Kapatma Kayıpları
İş gücünü Etkileyen 5 Büyük Kayıp
- Yonetim Kayıpları
- Üretim Hareket Kayıpları
- Hat Organizasyon Kayıpları
- Lojistik Kayıpları
- Ölçme ve Ayar Kayıpları
Malzeme ve Enerji Etkinliğini Onleyen 3 Buyuk Kayıp
- Enerji Kayıpları
- Jig, Kalıp ve El Aleti Kayıpları
- Ürün Kayıpları
Bu amaçla BİLTAŞ, Toplam Verimli Yönetim Sistemini uygulayan kurumlarda TPM’in temel taşlarından biri olan Kaizen işlemlerini bilgi işlem ortamında entegre bir sisteme dönüştürerek, kurumların Kaizen İşlemleri ihtiyaçlarını çözen BSOFTtpm Kobetsu Kaizen İşlemleri‘ni geliştirdi.
BSOFTtpm Kobetsu Kaizen İşlemleri, Toplam Verimli Yönetim Sisteminin sekiz temel yapı taşlarından biri olan Kobetsu Kaizen İşlemlerinin detaylı ve görsel olarak takip edilebildiği ve sonuçları ile ilgili analiz raporlarının oluşturulduğu, %100 web tabanlı bir yönetim modülüdür.
Özellikleri
- Uygulama Microsoft. NET teknolojisi ile tam nesne yönelimli olarak geliştirilmiştir.
- Öğrenmesi ve kullanımı son derece kolay bir kullanıcı ara yüzüne sahiptir.
- Sistem parametrik bir yapıyla tasarlanmıştır.
- Misyon-Vizyon tanımları.
- Kaizen ile ilgili hedefler.
- Komite Üye işlemleri.
- Öneri Kart İşlemleri.
- Kaizen işlemleri.
- Poke Yoke işlemleri.
- Önce sonra kaizen işlemleri.
- Sınırsız sayıda rapor dizayn edebilir, çıktılarını alabilirsiniz.
Otonom Bakım İşlemleri
Otonom Bakım, her işçinin kendi ekipmanı için temizlik, kontrol, yağlama, parça değişimi (kesici uç, filtre elemanı vb.), basit onarım (hortum kelepçesini sıkmak gibi), sorun giderme, doğruluk kontrolü ve bunlara benzer çalışmaları yaptığı, “kendi ekipmanının uygun koşullarını kendisinin sürdürmesi”ni amaçlayan faaliyetlerdir.
Çalışanın, kendi makinesine gönüllü olarak bakım yapması, hatta iyileştirmelerde rol alması fikri, TPM’in “kendi ekipmanına kendin bakım yap” görüşünün temelini oluşturmuştur
Otonom Bakım’ın tatmin edici seviyede yürütülebilmesi ve bazı bakım sorumluluklarının operatörlere devredilebilmesi için onları “makinelerinden anlayan” kişiler haline getirmemiz, eğitmemiz gereklidir. Bundan sonra, üretim elemanları sadece birer operatör olarak değil, bakım çalışanları olarak da hareket etme durumundadırlar. Fabrikalarda kullanılan ekipmanlar giderek nezaret gerektirmeyen, otomatik makinelere dönüşmektedirler. Dolayısıyla, operatörlerin makineleri ile ilgilenebilecekleri daha fazla zamanları olacaktır.
Otonom bakım 7 adımda uygulanır ve bir ekip çalışmasıdır.
- Makinanın günlük temizliği ve sorun belirtilerinin öğrenilmesi
- Kirlenmeyi engelleyecek yöntemlerin öğrenilmesi, zor ulaşılan yerlerin kolay ulaşılır hale getirilmesi
- İlk temizlik,inceleme ve yağlama standartlarının oluşturulması
- Kontrol prosedürleri hakkında genel eğitim yapılması
- Kontrolların “otonom” yapılmaya başlanması
- Standartların ve Görsel Yönetimin uygulanması
- Tam Otonom Bakımın başlaması
BSOFTtpm Otonom Bakım İşlemleri, TPM’in temel taşlarından biri olan otonom bakım işlemlerinin pratik, hızlı ve güvenilir bir şekilde takip edilmesini sağlayacak ve değişik raporlar üretecek şekilde geliştirilmiş web tabanlı bir uygulamadır.
Özellikleri
- Uygulama Microsoft. NET teknolojisi ile tam nesne yönelimli olarak geliştirilmiştir.
- Öğrenmesi ve kullanımı son derece kolay bir kullanıcı ara yüzüne sahiptir.
- Sistem parametrik bir yapıyla tasarlanmıştır.
- Sınırsız sayıda rapor dizayn edebilir, çıktılarını alabilirsiniz.
Misyon Vizyon
Otonom bakım ile ilgili yapılacaklar ve yapılma şekli tanımlanır. Gerekli durumlarda bunlar yenilenir.
Hedef
Otonom bakım ile ilgili hedefler belirlenir. Bu hedefler adım atlama ve benzeri yerlerde kullanılır. (Ne kadar öneri kartı asılacağı, ya da ne kadar olumsuzluk kartı asılacağı vs.) Hedefler ulaşılması durumunda puan dağıtımı ve sonraki adımlara geçiş için gereklidir.
Komite Üyeleri
Otonom bakım ile ilgili görevlendirme ve değerlendirme yapacak personelin seçimi yapılır. Bu personel çeşitli görevlerde için çalışacak personeli seçer. Ekipleri kurar ve bunları yönlendirir. Yapılan işler sonucu değerlendirmeleri yapar.
Yayılım Planı
Görev verilen gruplarım otonom bakım hedeflerine ulaşmaları için yapacakları işler ve sürelerin belirlenmesi. Belirlenen hedeflere ulaşmak için izlenecek yöntemler belirlenir, süre dışına çıkan planlar yeniden gözden geçirilir.
Ekip Üyeleri
Yayılım planını uygulayacak ve sorumlu olacak personelin seçimi. Personel Komite üyeleri tarafından eğitim ve yetkinliklerine göre seçilir. Gerekli görüldüğünde ekip üyeleri değiştirilebilir, eklenebilir çıkartılabilir.
Olumsuzluk Kartı Girişi
- Çeşitli lokasyon, makine ve araçlar ile ilgili personelin tespit ettiği ve ödül için puan aldığı olumsuz durumların bildirilmesi. Olumsuzluk kartı basılarak ilgili yere asılır. Bu kartlar herkes tarafında görülebilir. Olumsuzluk bildiren personel bunun ile ilgili puana alır.
- Olumsuzluğu gideren personel bu kartı kaldırarak olumsuzluğu nasıl giderdiğini bildirir. Ne zaman ve ne yaparak olumsuzluğu giderdiğini belirtir.
- Komite Üyeleri kaldırılan olumsuzluk kartlarını incelerler ve değerlendirirler. Gerekirse iyileştirmeyi iptal edip kartı tekrar aktif ederler.
- Onaylanan kartlardan dolayı iyileştirme yapanlar puana kazanırlar
Toplantı Kararları
- Çeşitli zamanlarda yapılan toplantılara, katılacakların belirlenmesi ve toplantıda alınan karaların kaydı yapılır.
- Toplantı zamanı, konusu ve katılacaklar belirlenir.
- Toplantıya katılmayan personel çıkartılır.
- Toplantı sonunda çıkan karalar kaydedilir.
Kirlilik Kaynakları
- Kirliliğe sebep olana lokasyon, makine ve araçların tespiti ve derecelendirmesi yapılır.
- Kirlilik için olması gereken en az değerler belirlenir.
- Hali hazırda olan kirlilik tespit edilir ve bu kirliliğin düşürüleceği seviye belirlenir
- Olması gereken değer ve bu değere ulaşmak süresi tanımlanır.
Adım Atlama Denetleme
- Yayılım planının başarı ile uygulanmasının denetlenmesi. Belirtilen şartlardaki başarı puanlarının değerlendirilmesi yapılır.
- Yayılım planı için değerlendirilecek maddeler belirlenir. Bu maddeler çeşitli gruplar altında toplanabilir.
- Bu maddelerin her birine yayılım planının uygulanmasındaki başarı oranında puan verilir.
- Bu puanlar toplanarak belirlene hedefe göre adım atlama işleminin gerçekleşip gerçekleşmediği tespit edilir.
- Adım atlama gerçekleşmişse yeni yayılım planı hazırlanır ya da hali hazırda olan biri ekibe verilir.
Ulaşılması Kontrolü ve Bakımı Zor Bölgeler.
- İşletme içinde bulunan kontrolü ve bakımı zor olan yerlerin tespiti yapılır.
- Bunlar ile ilgili belgeler (Fotoğraf vb) toplanır.
- Bakımının ve kontrolünün zor olmasının sebepleri belirlenir.
- Belirlenen sebepler giderilmeye çalışılır, sonra tekrar kontrol edilip belgelenir
Sorumluluk Paylaşımı
- Belirlenen otonom bakım işlemleri için yapılan planlara sorumlu ve departman atama işlemleri yapılır.
- Sorumlu ve departman otonom bakım ile ilgili bölümlerden seçilir.
- Yapılacak işler ve plan belirlenir ve bu palanın gerçekleşmesi,için gerekli süre bildirilir.
Ramak Kala
- İş kazasına sebep olabilecek durumların belirlenmesi yapılır. Belirlenen durum ilgili yere kart asılmak sureti belgelenir.
- İş kazası grubu tespit edilir ve bu iş kazasına yol açabilecek şartların ne olduğu detaylı olarak açıklanır.
- Kaza riskini ortadan kaldıran personel kartı kaldırır.
- Kaldırılan kart komite üyeleri tarafından değerlendirilir, uygun bir çözüm olmadığına karar verilirse kart yeniden aktif edilir.
- Eğer kart kaldırılması komite tarafından onaylanırsa, bildiren personel ve ramak kala durumu için iyileştirme yapan personel puana kazanır.
5S İşlemleri
5S metodolojisi çalışanların bilinçlenmesini sağlayarak, hedeflenen kazanımları elde etmiş ve sürekli iyileştirmeye açık bir sisteme sahip işletmeler oluşturmayı hedefler. 5S iş güvenliği, kalite, verimlilik, makine performansı, stok kontrolü, çalışanların katılımı ve motivasyonuna büyük katkılarda bulunan basit ve kolay uygulanabilen, çalışanlara uygulatılan değil, bizzat çalışanlar tarafından uygulanan bir sistemdir. 5S çalışanlara keyifli ve güvenli çalışma koşulları sağlar, işyerine ‘’ait olma’’ duygusunu hissettirir, ‘’benim saham, benim makinam ve benim fabrikam’’ bilincini aşılar ve ekip çalışmasını geliştirir.
İsmini, sistemi oluşturan 5 adımın Japonca baş harflerinden alan 5S metodolojisi, kendi kendini yöneten sihirli bir sistem değildir. Etkili olabilmesi için şirketteki herkesin tekrar tekrar bu sistemi uygulaması gereklidir. Uygulamada istenen başarının elde edilmesi ve sürekliliğinin sağlanması için şirketin üst yönetiminden operatör seviyesine kadar herkesin metodolojiye inancı ve desteği şarttır.
5S Adımları:
1.Adım SEİRİ (Toparlama-Ayıklama)
Ayıklama adımında saha detaylı bir şekilde gözden geçirilerek gerekli ve gereksiz malzeme, stok malzeme, demirbaş, el aleti vs. birbirinden ayırılır. Bu malzemeler genelde bir gün lazım olur diye tutulmuş veya bozulmuş ancak elden çıkarılmamış malzemelerdir.
Ayıklanan bu gereksiz malzemeler bir alana toplanarak değerlendirme yoluna gidilir. İlk yapılması geren ilgili tüm birimlerin bu malzemelerden haberinin olmasını sağlamak ve ihtiyacı olan departmanlara vermek olmalıdır. Geriye kalanlar ise hurda olarak satma, bağışlama vs. Tasnif yöntemleriyle elden çıkarılır. Bu adım binanın temeli gibidir, mümkün olduğu kadar sıkı uygulanmalıdır.
2.Adım SEİTON (Düzen)
Düzen adımı sürekli ihtiyaç duyulan tüm malzeme, demirbaş, el aleti vs. için adresleme yapma adımıdır. Amaç ihtiyaç duyulan tüm malzemelere mümkün olan en kısa sürede ulaşmak, alınmasını ve bırakmasını kolaylaştırmak olmalıdır. Bu adımda tüm bu malzemeler çalışma alanına en yakın şekilde ergonomi ve iş güvenliği göz önünde bulundurularak düzenlenir, yerleştirilir, işaretlenir ve minumum ve maksimum stok seviyeleri belirlenerek sipariş ve stok miktarlarına karar verilir.
3.Adım SEİSO (Temizlik)
Temizlik adımının amacı çalışma alanındaki bütün toz ve kirliği ortadan kaldırmak ve tertemiz tutmaktır. Çalışanlar kendi alanlarını temizliğinden sorumlu olmalıdırlar, ancak zamanlarını büyük bölümünü de temizlik yaparak geçiremezler. Bu adımda sahasını tanıyan çalışan tüm kirlilik kaynaklarını tespit eder ve kaizenler yaparak iyileştirme yoluna gider.
Her bölümün ve alanın bir sorumlusu olur. Çeşitli temizlik yöntemleri geliştirilerek standartlaştırma yoluna gidilir.
4.Adım SEİKETSU (Standartlaştırma)
Bu adım ilk üç adımda elde edilen başarıların (çalışmaların) sürekliliğini sağlamak ve sahaya yansıyan bu olumlu durumun sürdürülmesi için oluşturulacak standartlar, iyileştirmeler ve kontrol yöntemleridir. Üç ana amacı vardır;
- Sıfır Karışıklık
- Sıfır Gereksiz parça
- Sıfır Kirlilik
Saha yukarıdaki üç başlık dikkate alınarak yürüyen sistemin sorgulanması gereken noktalarını tespit eder ve iyileştirme faaliyetlerini yürütür.
5.Adım SHİTSUKE (Disiplin)
5.Adım kurallara bağlılığın alışkanlık haline getirilmesi, faaliyetleri geliştirmek ve sürekliliğini sağlama adımıdır. Herkes her an çalışma alanını ve ekipmanını denetlemeli ve yeni katılan her ekip üyesine gerekli eğitimi vermelidir. Çalışma alanı artık kendiliğinden harekete geçmelidir.
Disiplin adımının faydaları;
- Çalışanların sorumluluk bilincini geliştirir
- Çalışanların özgüveni artar
- Çalışanın rolleri belirlenir
- Çalışan varlığını hissettirir
- Geriye dönüşler yaşanmadığı için faaliyet kaybı yaşanmaz
- Çalışanların motivasyonu artar
BSOFTtpm 5S İşlemleri, komite üyelerinin tanımlarının yapıldığı, denetleme sorularının oluşturulduğu, 5S kartlarının girişlerinin yapıldığı ve denetleme sonuçlarının analiz edildiği web tabanlı bir uygulamadır.
Özellikleri
- Uygulama Microsoft. NET teknolojisi ile tam nesne yönelimli olarak geliştirilmiştir.
- Öğrenmesi ve kullanımı son derece kolay bir kullanıcı ara yüzüne sahiptir.
- Sistem parametrik bir yapıyla tasarlanmıştır.
- Sınırsız sayıda rapor dizayn edebilir, çıktılarını alabilirsiniz.
OEE Üretim Detay İşlemleri
OEE (Overall Equipment Effectiveness – Toplam Ekipman Etkinliği), üretim süreçlerinizin (ör: makineler, üretim hücreleri, montaj hatları) etkinliğini, gözleyebileceğiniz ve geliştirebileceğiniz, “en iyi deneyimler” yoludur. OEE, basit ve pratiktir. En önemli ve yaygın üretim verimliliği kayıpları kaynaklarını alır, bunları üç ana kategoriye yerleştirir ve metriklere ayrıştırır. Ki bu metrikler nerede olduğunuzu ve nasıl gelişeceğinizi ölçmek için mükemmel ölçüm altyapısı sunar.
OEE, sık sık, TPM (Total Productive Maintenance – Toplam Verimli Bakım) ve yalın üretim programlarında anahtar metrik olarak kullanılır. TPM’in ve diğer girişimlerinizin etkinliğini, ölçebilmeniz için üretim etkinliğini ölçen genel bir çatı sağlayarak, tutarlı bir yol sunar. OEE, gerçekten, karmaşık üretim problemlerini, basit, anlaşılabilir bilgi haline getirir. Basit ölçümlerle, süreçlerinizi sistematik olarak geliştirmenizi sağlar.
Altı Büyük Kayıp
OEE ve TMP programlarının ana hedefleri “Altı Büyük Kaybı” (Üretimde verimlilik kaybına yol açan en gelen nedenler) indirmek veya yok etmektir. Altı Büyük Kayıp;
- Arızalar
- Setup ve Ayarlamalar
- Küçük duruşlar
- Düşük Hız
- Başlangıç Retleri
- Üretim Retleri
BSOFTtpm Üretim Detayları İşlemleri, TPM’in başarısı için üretim etkinliğini ölçen genel bir çatı sağlayarak, tutarlı bir yol sunan ve karmaşık üretim problemlerini, basit, anlaşılabilir bilgi haline getiren, basit ölçümlerle, süreçlerin sistematik olarak geliştirilmesini sağlayan web tabanlı bir uygulamadır.
Özellikleri
- Uygulama Microsoft. NET teknolojisi ile tam nesne yönelimli olarak geliştirilmiştir.
- Öğrenmesi ve kullanımı son derece kolay bir kullanıcı ara yüzüne sahiptir.
- Sistem parametrik bir yapıyla tasarlanmıştır.
- Sınırsız sayıda rapor dizayn edebilir, çıktılarını alabilirsiniz.
OEE Çevrim Süreleri
Ürünün belirtilen hatta ne kadar sürede üretildiği belirlenir. Ürünler her hatta farklı sürede üretilebilir, işletmede
her hat için ürünün ne kadar sürede üretildiği tespit edilir ve bu değer sisteme girilir.
Durma Sebepleri
Üretim esnasında oluşan durma sebepleri belirlenir. Bu durma sebeplerinin bazıları OEE içine dahil edilir bazıları ise OEE hesabında kullanılmaz.
Burada durma sebepleri arıza, bakım, yapılandırma gibi makine kaynaklı olabileceği gibi elde olmayan sebepler (Elektrik kesintisi vb) veya iyi planlanmamış işler sebebiyle olabilecek hammadde sıkıntısı bile olabilir.
Gerekli tüm durmalardan sonra oluşan eksik oran ise performans belirlemede kullanılabilir.
Üretim Raporları
- Çalışma periyodu içerisinde üretilen ürünler ve bu periyotta duruş süreleri girilir. BU girişler ile OEE yüzdesi belirlenir, eğer istenirse ve yeterli sıklıkta üretim ve durma giriliyorsa gerçek zamanlı OEE takip edilebilir.
- Periyot sonunda bu çalışma süresinin ne kadar verimli geçtiği hesaplanır. Bu kaba bir hesaptır, dahil hariç durma süreleri ile yüzde hesaplanır.
- Çalışma sonunda detaylı bir üretim raporu çıkartır. Bu raporda hangi üründen ne kadar üretilmiş, ne kadar hatalı, ne kadar tekrar tamir edilip kullanılabilir ürün çıkmış gözükür. Bu rapor değişik durumlara göre esnek bir şekilde değiştirilebilir.
Üretim Göstergeleri
- Tarih, hat ve vardiyaya göre çeşitli şekillerde OEE yüzdesini gösteren kadranlardır.
- Böylelikle yönetici her hangi bir anda işletmedeki anlık verimliliği görsel olarak görebileceği gibi, geçmiş zamanlardaki çeşitli birimlerinde durumlarını görebilir.
Biltaş ile Dijital Dönüşüm Yolculuğunuza Başlayın
İş süreçlerinizi optimize edecek akıllı yazılım çözümleriyle tanışın ve verimliliğinizi artırın.